To other TR6 pages
February 16, 2014
Rocker Arms
The
rocker gear was great fun to work on. It's very machine-like,
with all those levers and joints, and it's one place where small
changes can make a significant difference in the performance of the
engine. The rockers' job is to transfer information from the cam lobes to the valves.
In
taking everything apart, there was a lot of evidence of heavy wear.
the rocker shaft was deeply scored under some of the rockers, and
many of the rockers showed heavy wear, too.
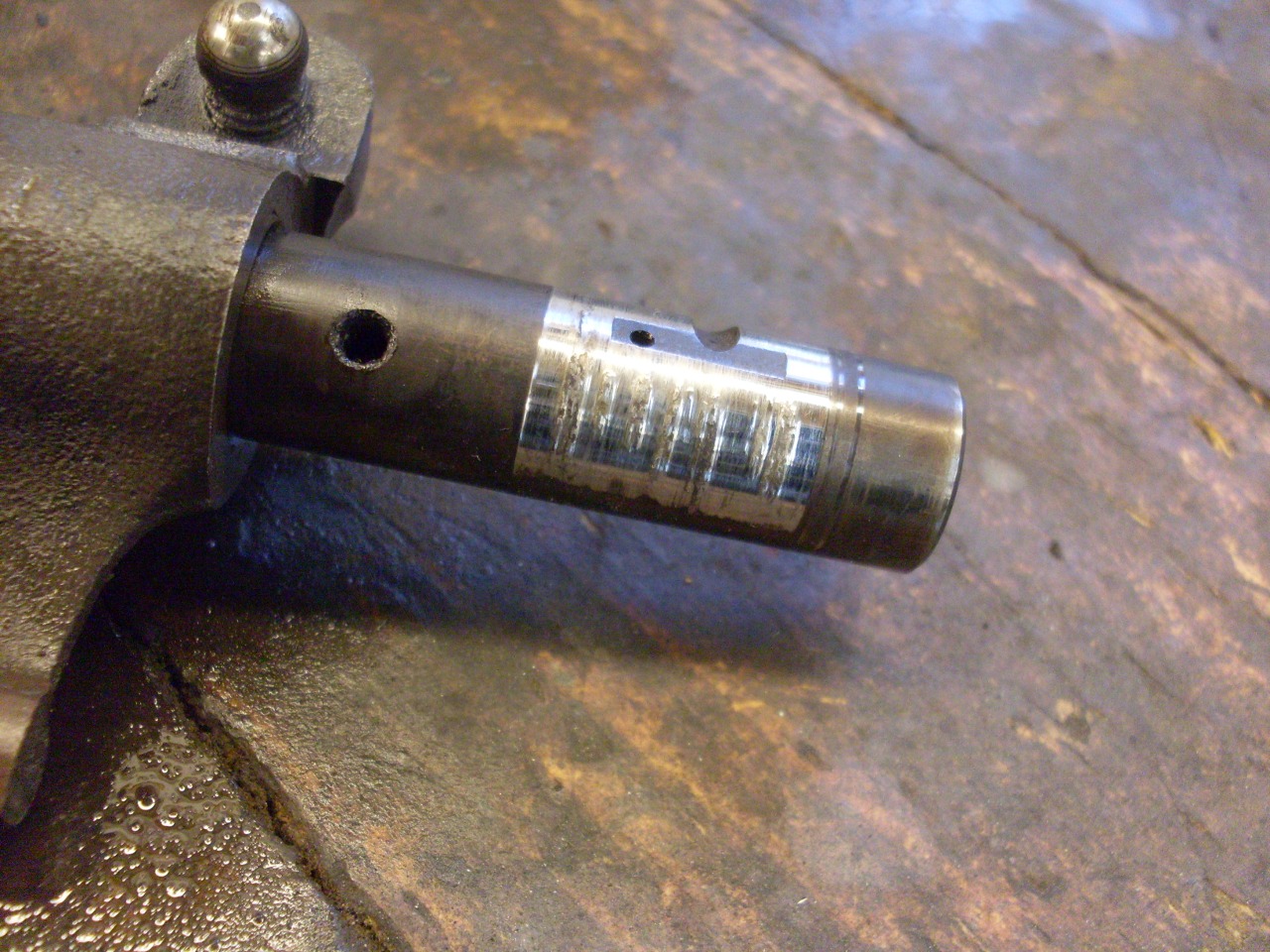

One
interesting thing was that the rocker shaft showed significant wear on
its top side where it is held by some of the pillars. The only
way I can explain this is that the shaft was twisting quite a bit.

Well, the shaft was definitely a gonner, so I got a new one.

But
then I started thinking about the rockers themselves, since they
certainly couldn't be used in their current condition. I'd much
rather see bronze bushed joints in this application, and there are
sources for bushed rockers. There is also at least one outfit
that will bush existing rockers, and this got me thinking whether this
was something I could do. I think the bushed rockers run around
$16-$18 each, so it's not really a huge-ticket item, but the challenge really
appealed to me.
Bushing a hole is not rocket science--you
drill the hole out to rough size, then ream it to a few thousandths
smaller than the bush OD, then press the bush in. This situation was
going to be a little more complicated, though. For one thing, I
was a little worried about removing much material from the bottom of
the rocker, where it is pretty thin--only about 0.150". I thought
boring the rocker for a 0.062" wall bush was taking too much. I
was much more comfortable with a bush with a 0.031" wall thickness, but
couldn't find the right size commercially. I finally decided to
open up the rocker bore by 0.062" (remove 0.031" all around), press in
a 0.062 wall bush, then bore and ream the bush.
The other
thing that makes this job a little more interesting is work holding.
I had to figure a way to securely hold an odd-shaped piece
so it can't shift or rotate. I have a small mill, but the
process I ended up with could also be done on a decent drill press.
I made a little fixture that I held in the mill vice.
The fixture had two clamps on it, one for each side or the
rocker. Luckily, these rockers have one flat side. There
was also a stud that one arm of the rocker would rest against to keep
it from turning.

The
rocker was drilled and reamed oversize, the bush was pressed in, and
the bush was drilled and reamed, all without moving or removing the
rocker from the fixture. This keeps everything concentric.
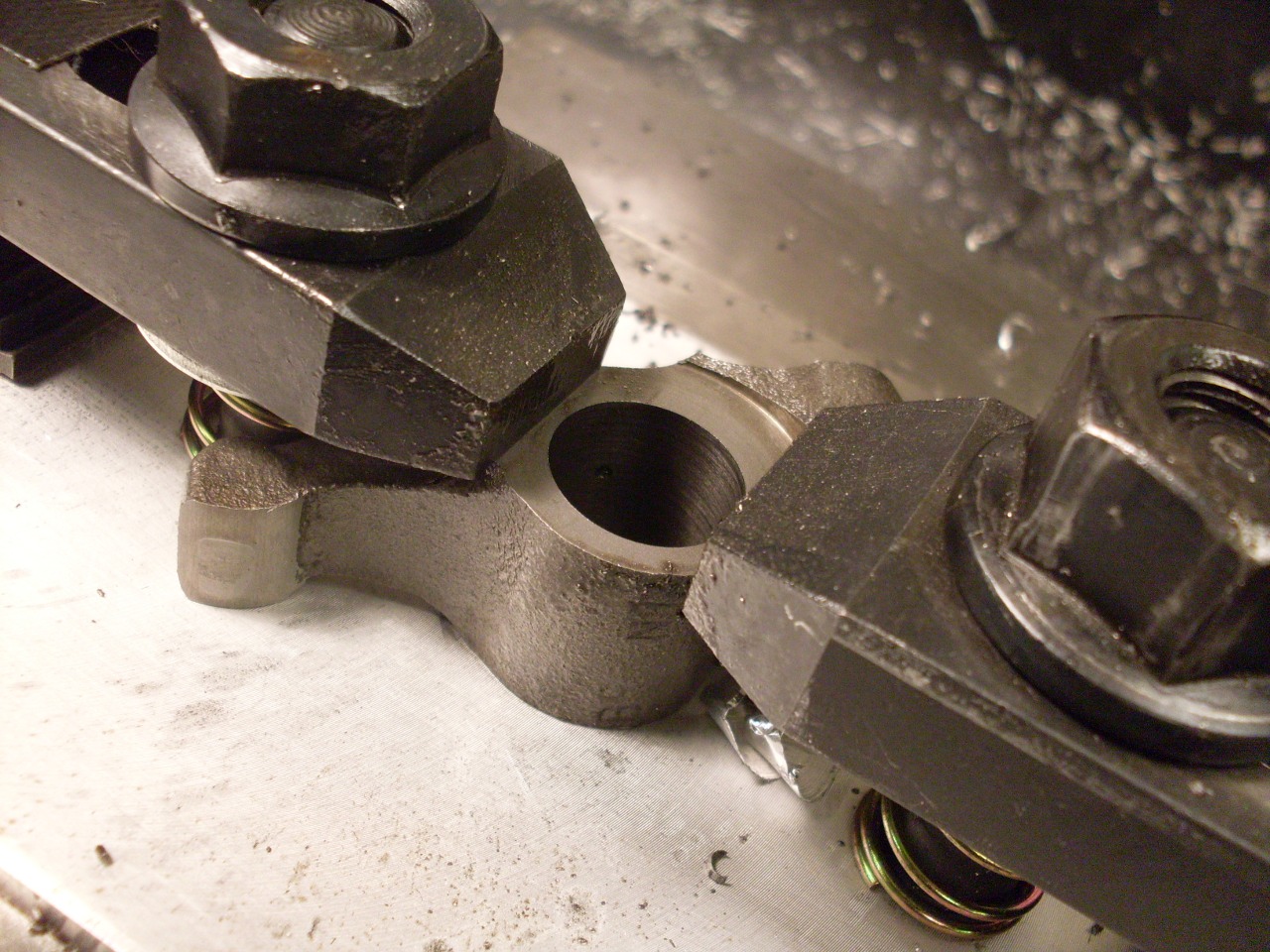

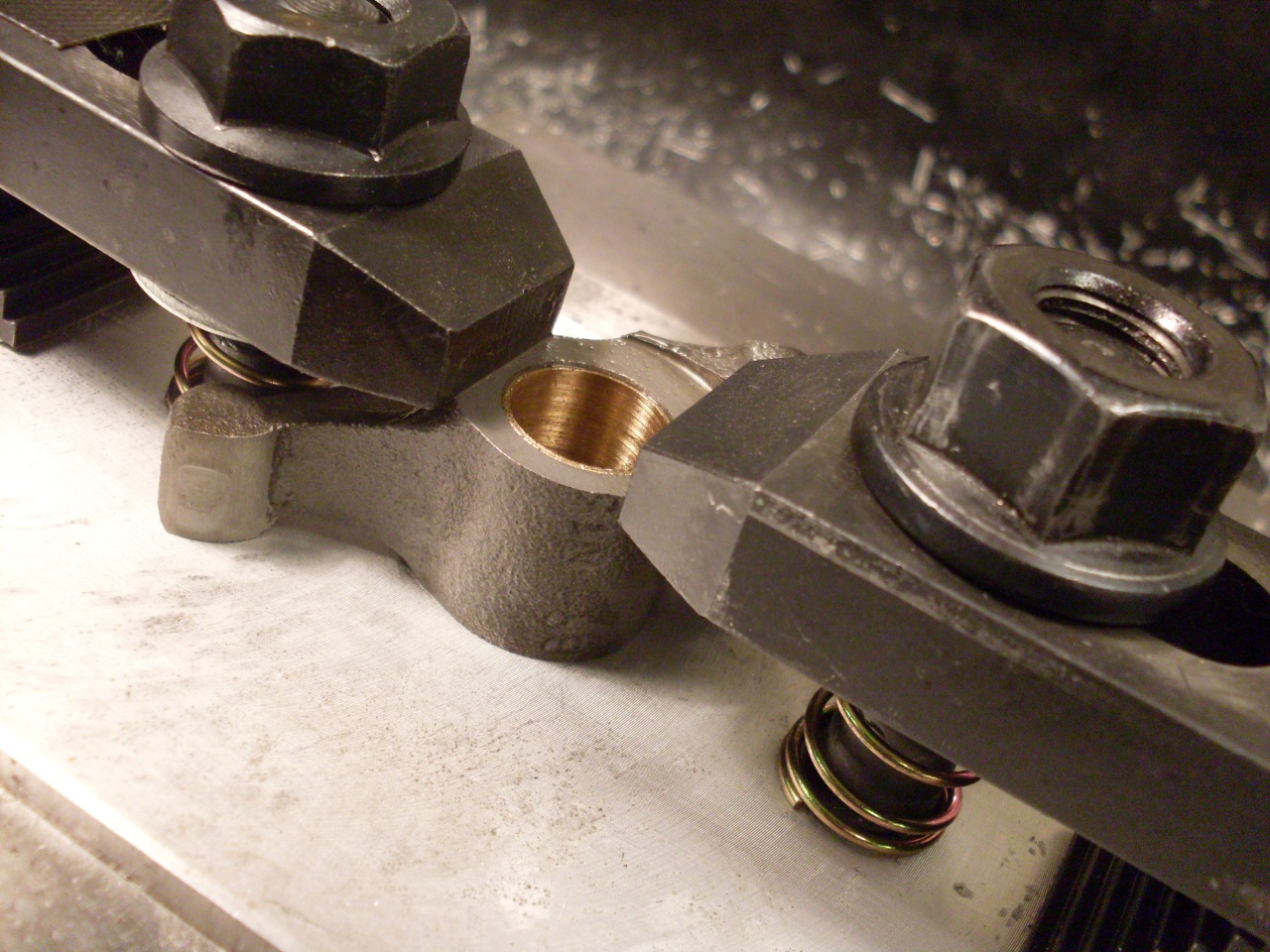
Then the bushes were chamfered. I had to move the rocker for this to do both sides.

The results looked pretty good:
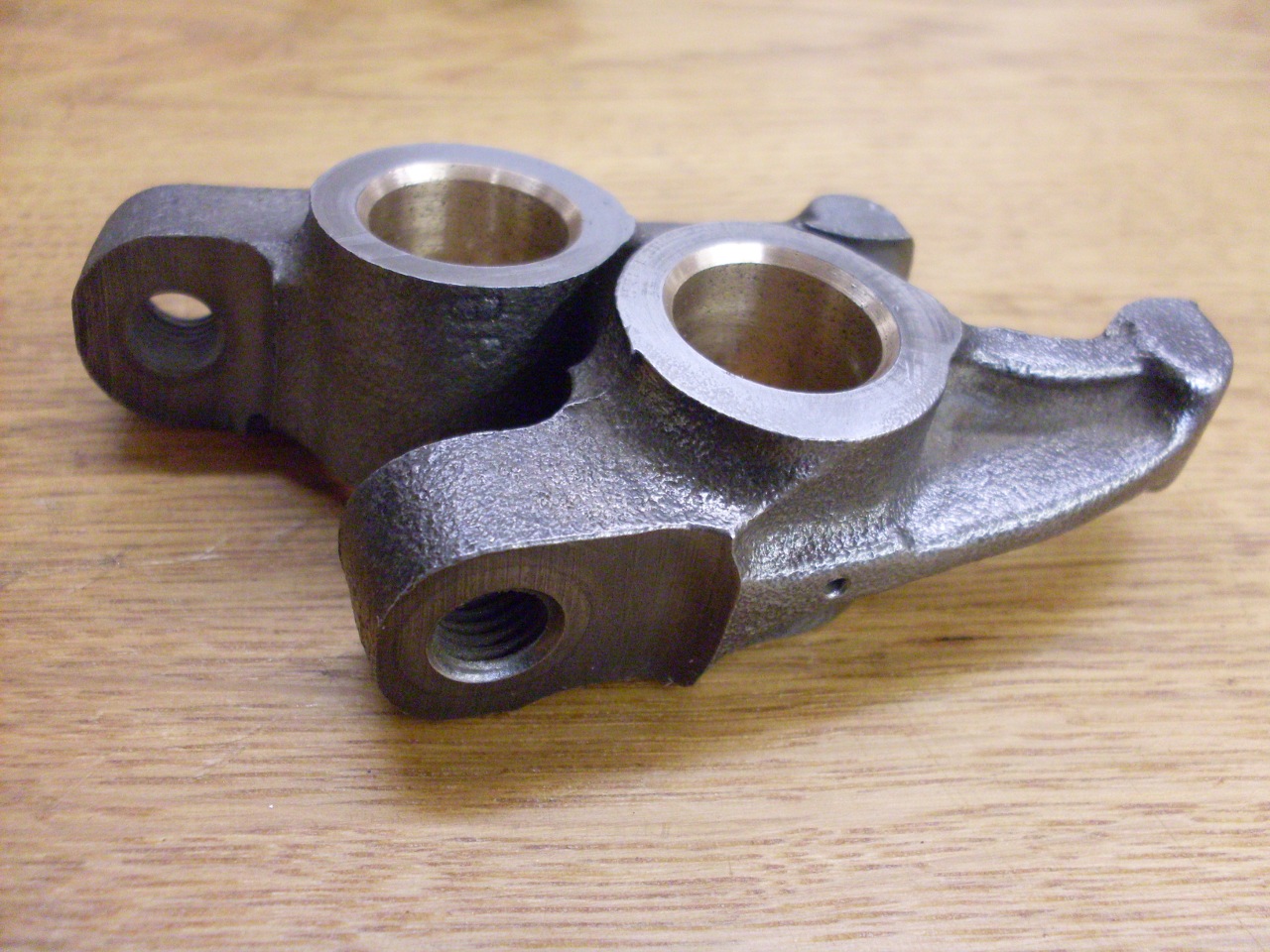
Then had to drill the two oil holes in each piece. The holes are different sizes.

I really considered this a success. After I got everything set up, the bushing only took a couple of hours.
My
back-patting was cut short when I realized that these rockers still
looked like used items as evidenced by the deeply worn patches on the
shoes (the parts that contact the valve stems).
This took
considerably more thought than the bushes. The rocker shoes
appear to be circular arcs with about a 5/16" radius.
After a lot of doodling, I made up this little jig that
holds the rocker bore vertical, and allows it to rotate around the
center of the shoe arc. The ball screw controls how much material
is removed. The whole jig is clamped to the table of my little 1
inch belt sander so that as the fixture is rotated, the shoe is
resurfaced. I only took off enough material so that the wear
marks just disappeared. From the point where the shoe was first
barely touching the belt to where the deepest of the worn areas was
gone only took about 1/4 turn of the 24-pitch adjustment screw,
indicating that at most, about 0.015" was removed.
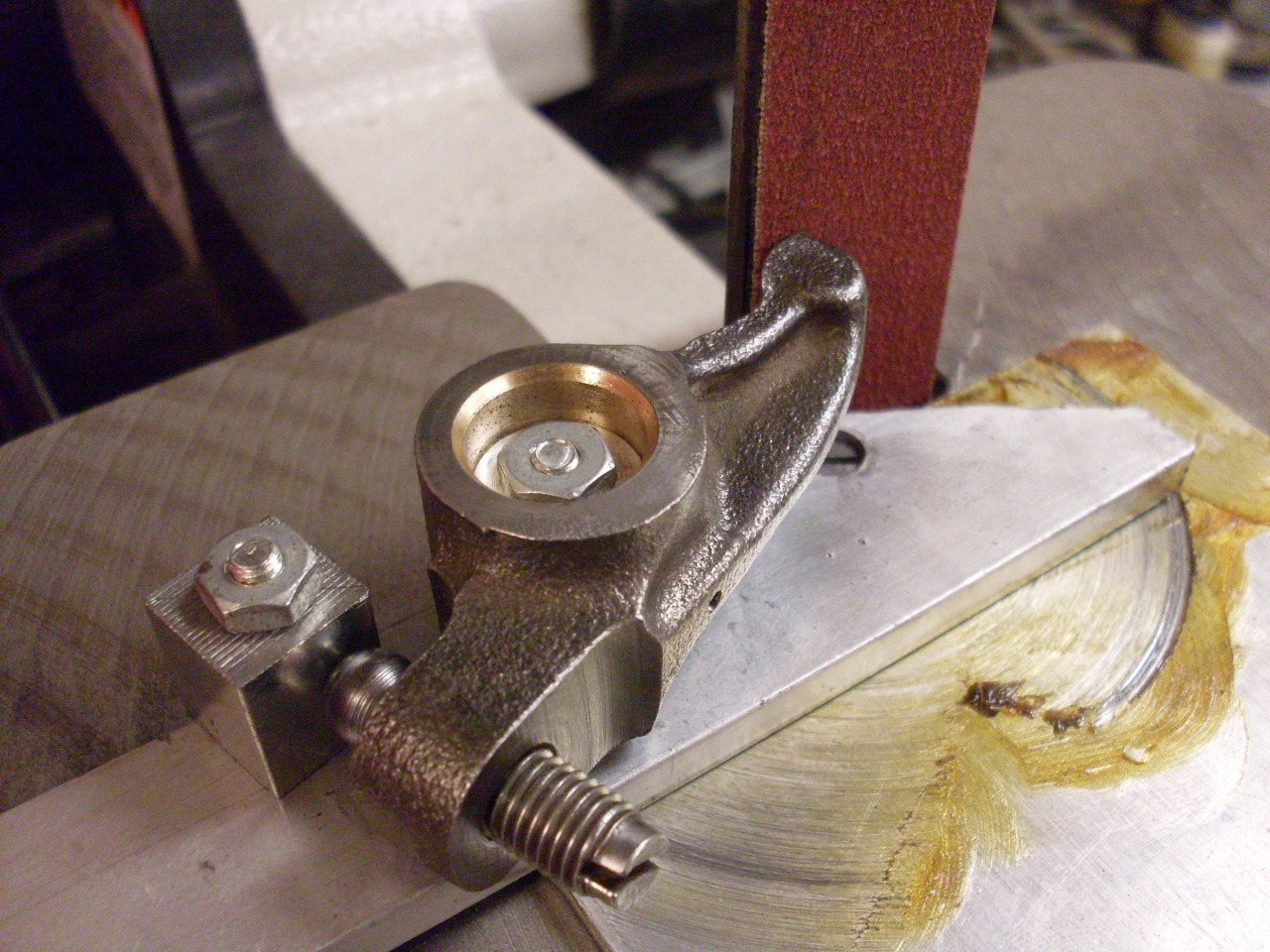
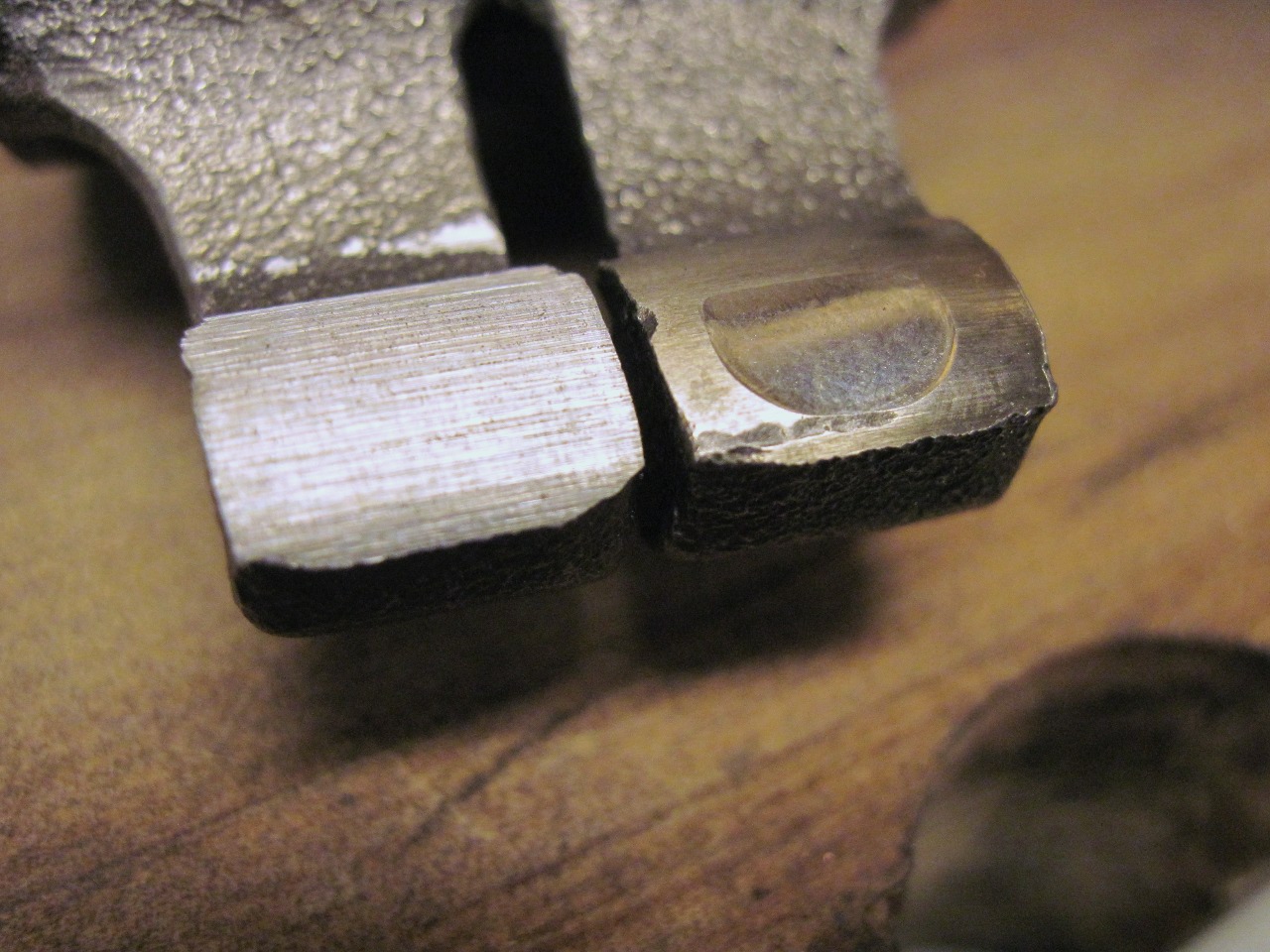
I thought the finish looked a little rough (120 grit on the belt), so I honed the surfaces with a fine stone.
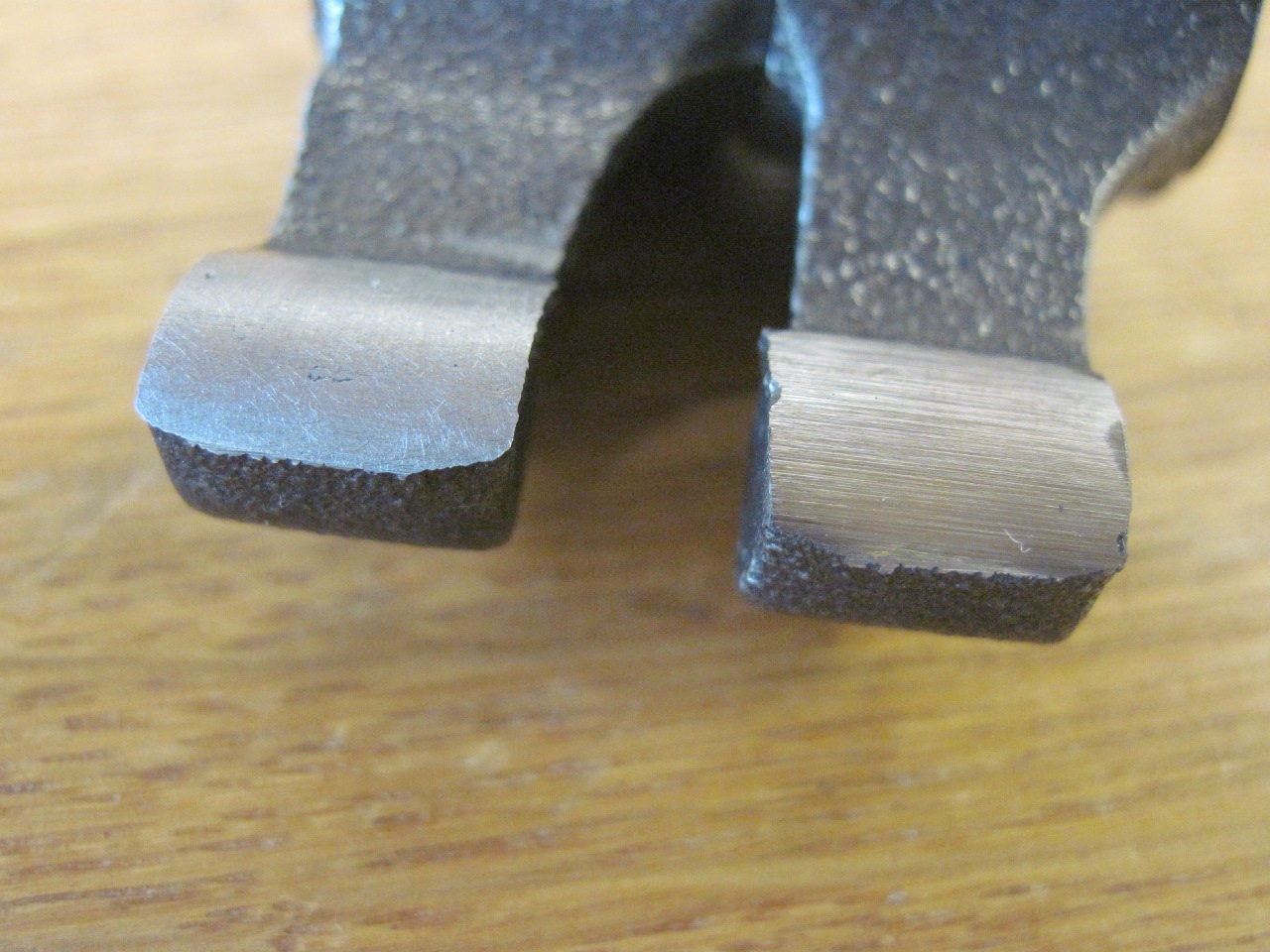
These
rockers were quite a lot of work, and the drills and reamers added up
to maybe half of what new bushed rockers would have cost. But, on the
other hand, for the $100 or so, I got the rockers AND the tools, not to
mention some pleasant shop time, some good experience, and a story to
tell.
Next up is trying to get a handle on the valve geometry.
Comments to: elhollin1@yahoo.com
To other TR6 pages