To my other MGA pages
March 2, 2025
Intake Manifold
The MGA intake manifold is a pretty unremarkable item. It's an
aluminum casting that includes two intake runners, each serving a pair
of cylinders, and a balance tube that connects them. Several
similar manifolds were used for the MGA, this one being the AEH174.
My manifold was dirty, but apparently intact. Being aluminum, many
owners take the time to polish their manifolds to some degree, and I'm
one of them, but this was done back in the 70s.
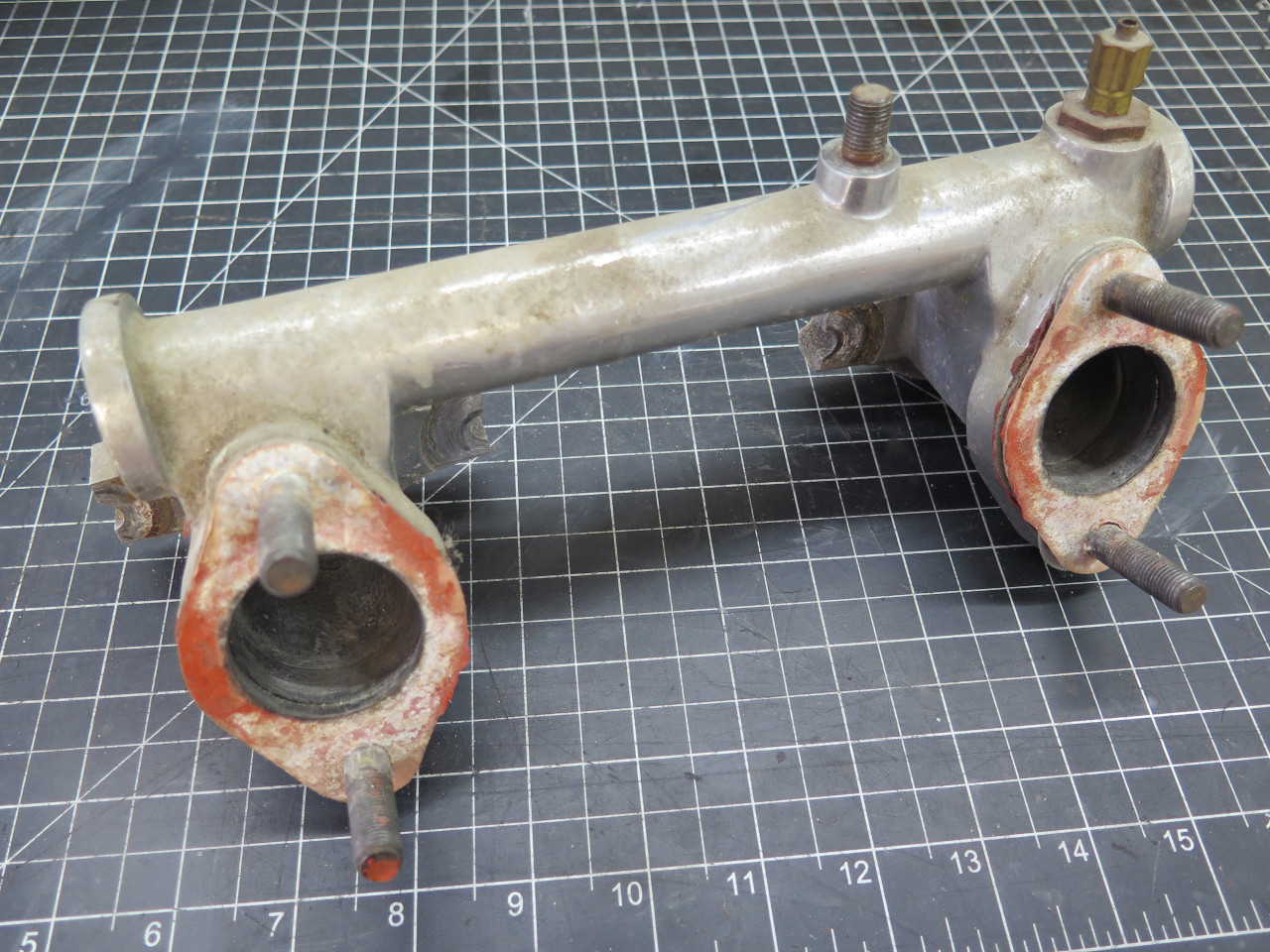
I pulled out all of the studs in preparation for the rehab. There
was a threaded opening in the balance tube that looked like it was
intended as some sort of vacuum port. It held a brass tube fitting
that apparently isn't stock. I believe I used it for a vacuum
gauge.
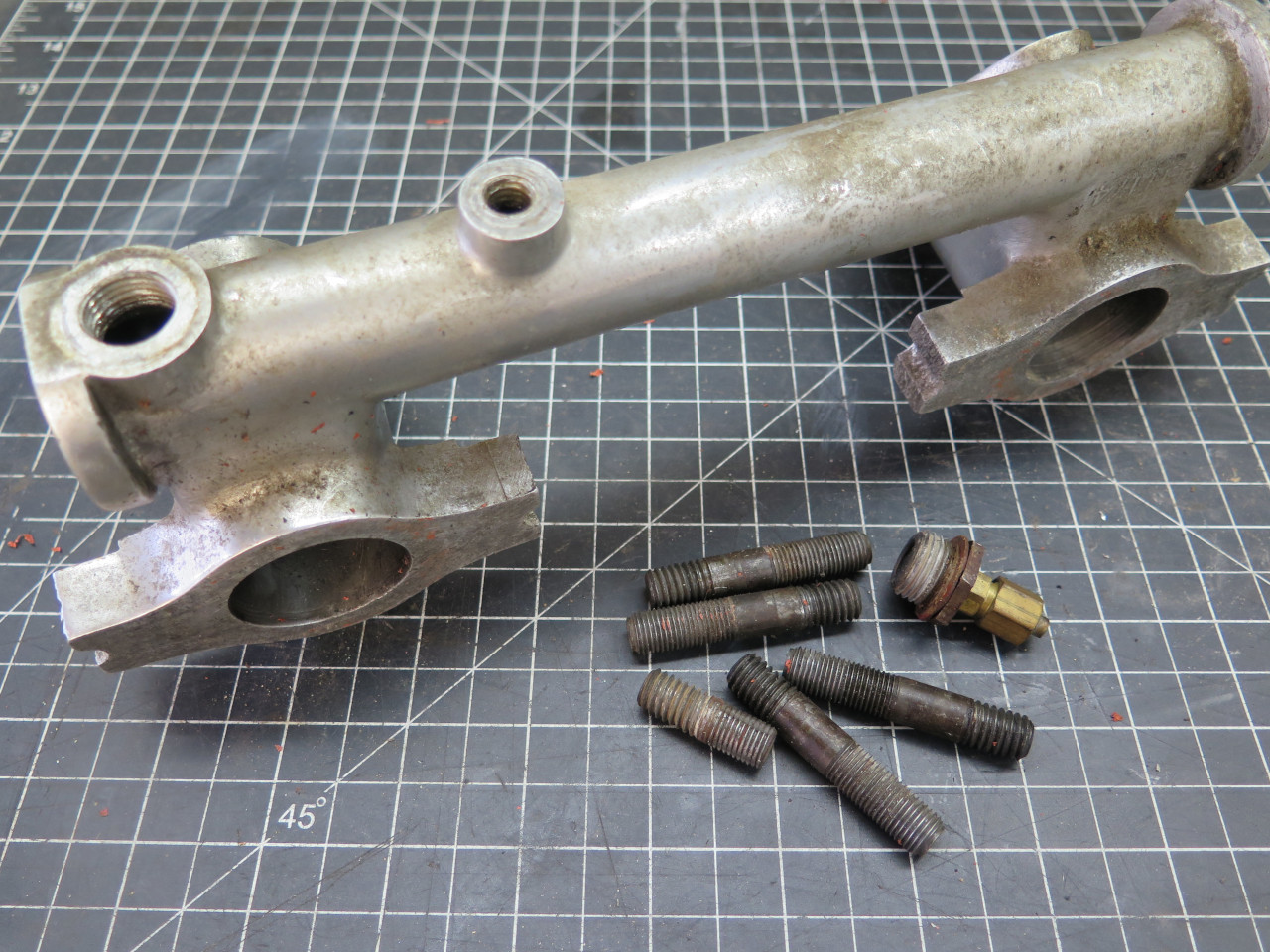
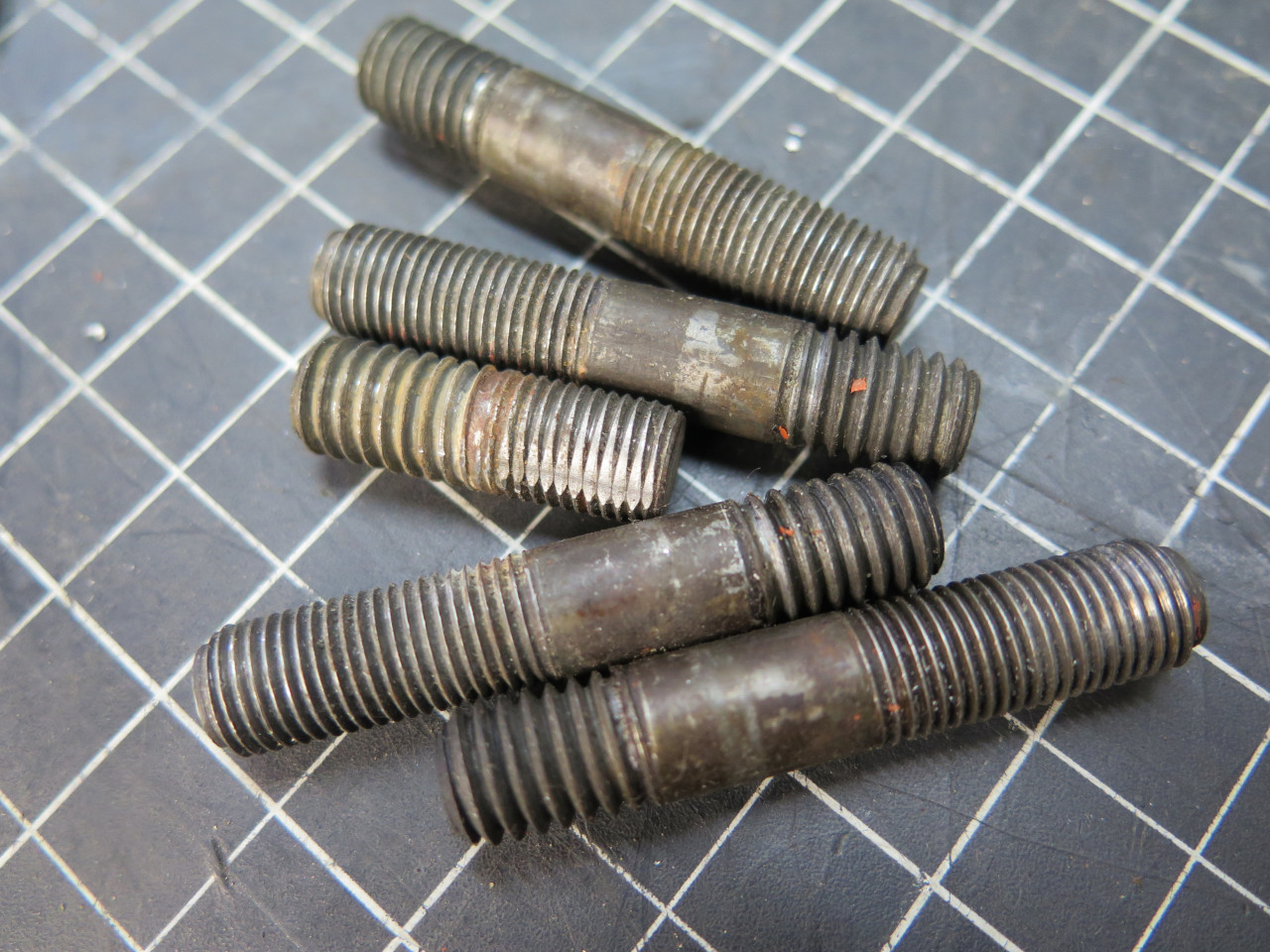
Some soap and water got rid of the dirt and grime.
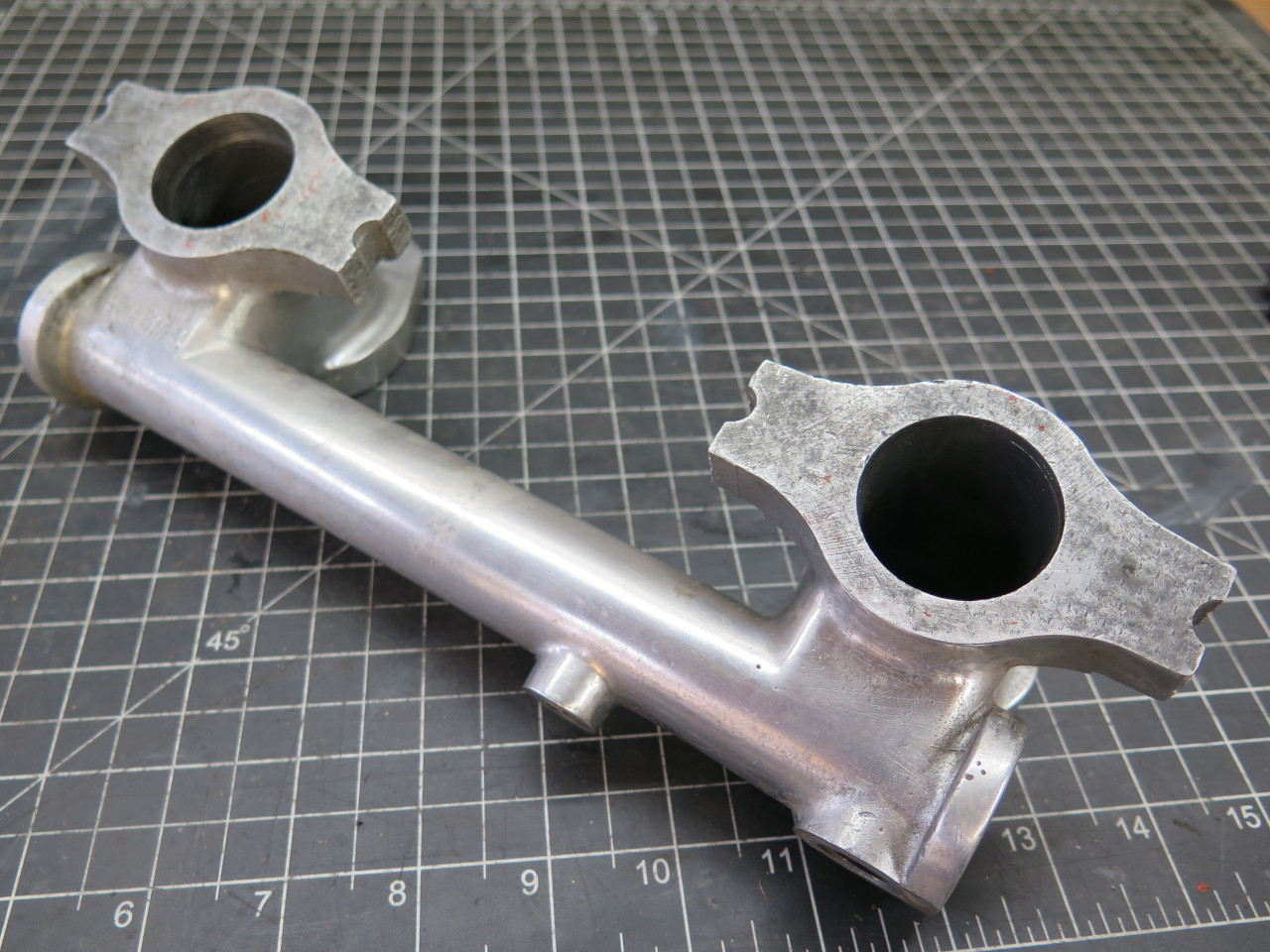
About the only thing that can be done to this part to improve its
performance is to smooth the internal runner surfaces. This will
not unleash any significant hidden horsepower, or probably even make any
noticeable difference in normal driving. But on the other hand,
it's fairly easy to do, and doesn't cost anything, so why not?
There were various bumps and ridges in the bores, but nothing major.
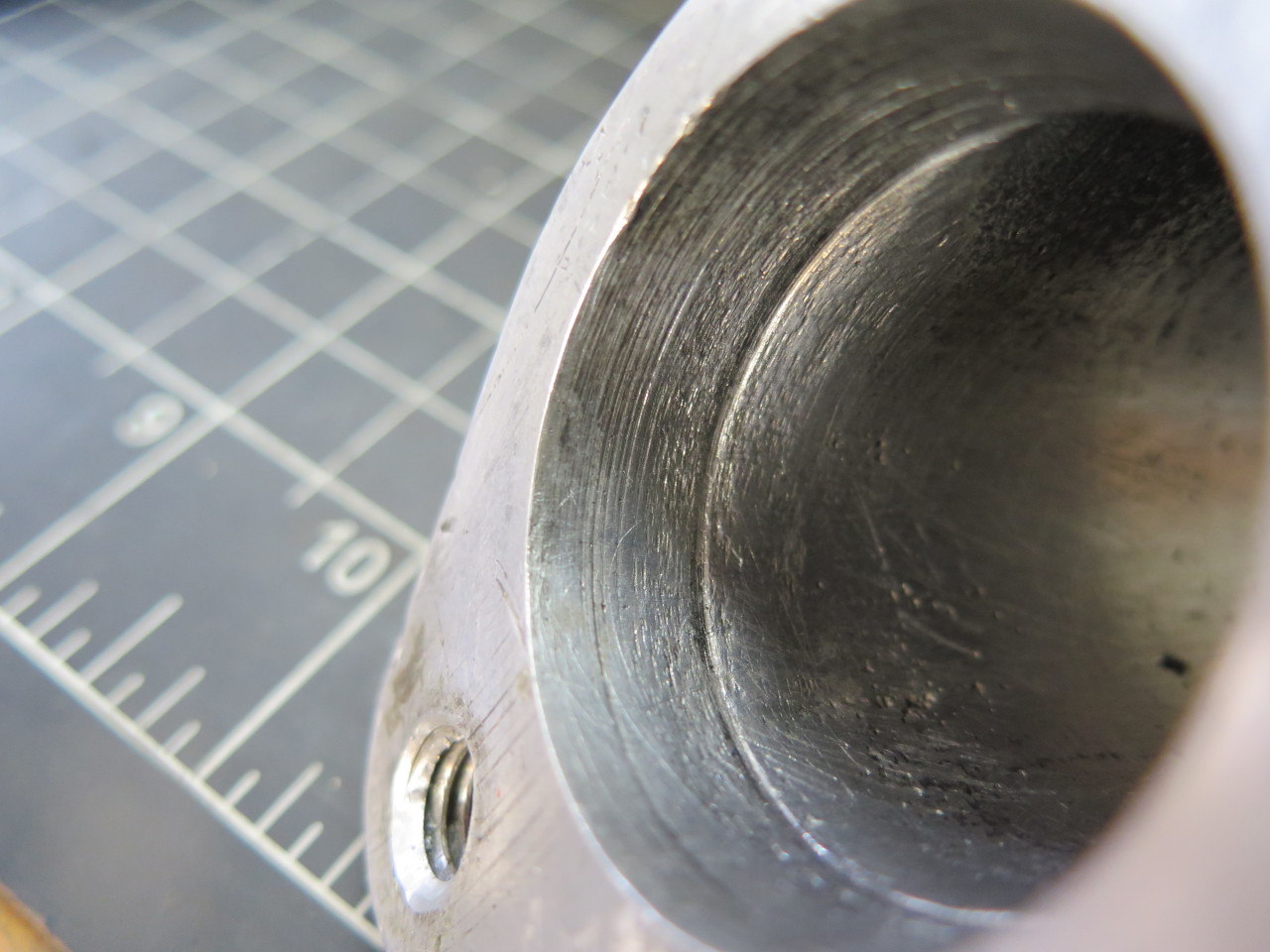
A preliminary check is to see of the head side port openings match the gasket. They did.
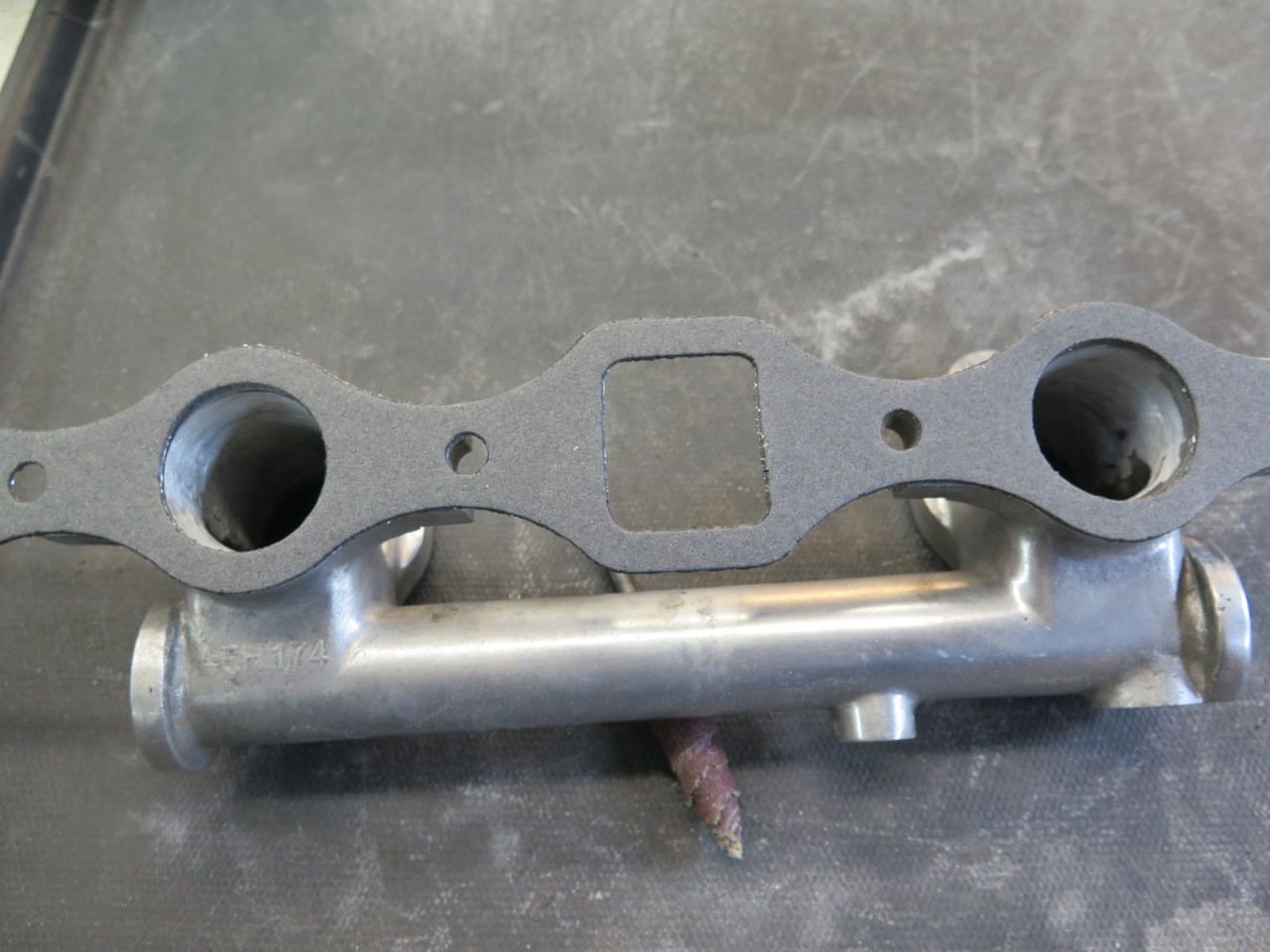
Then, with various abrasive implements and a flexible shaft tool, the
inside surfaces were blended into a pleasing smoothness. Current
thinking apparently holds that intake runners should not be polished,
but just smoothed. These surfaces were finished to about 80 grit.
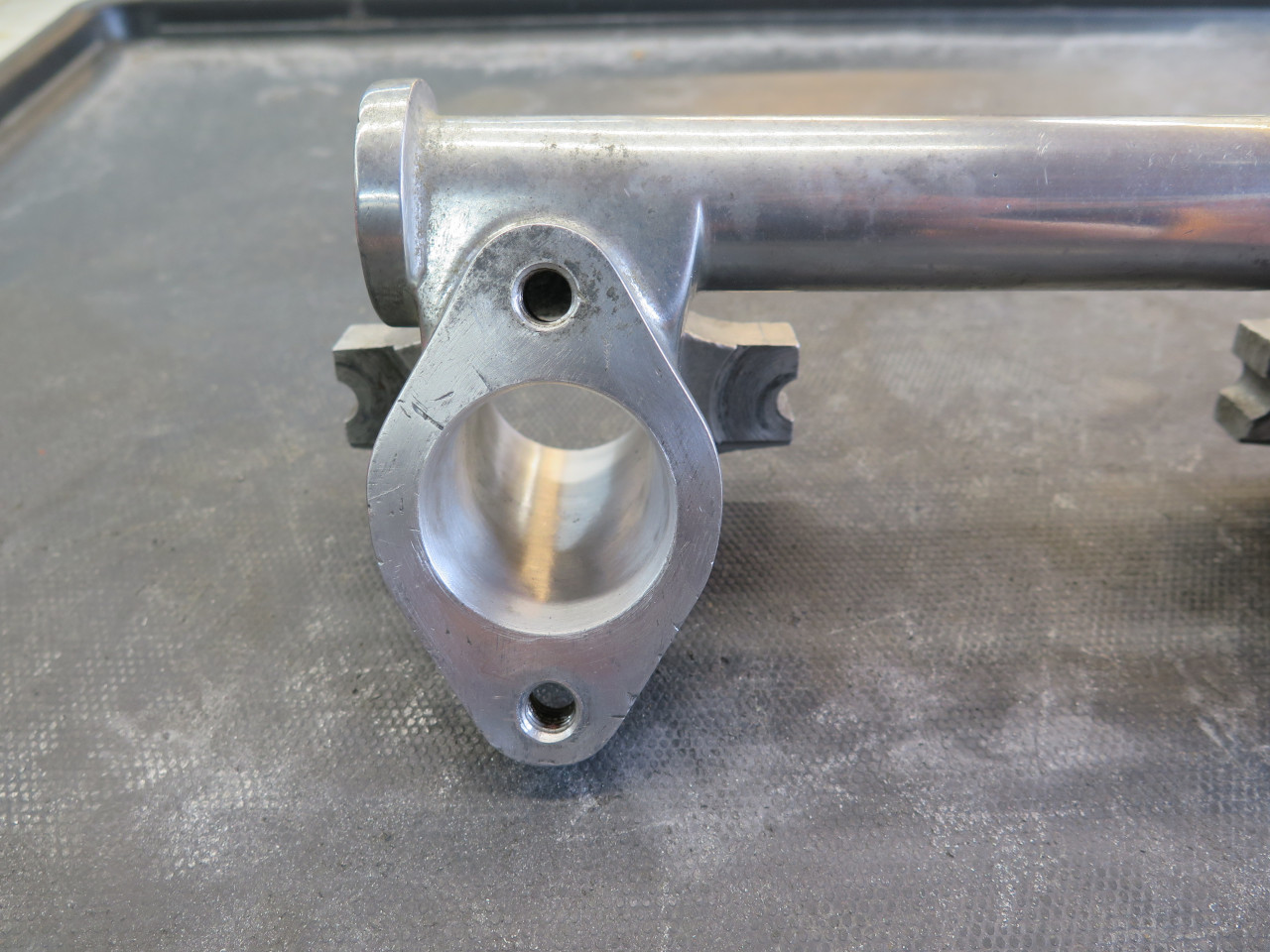
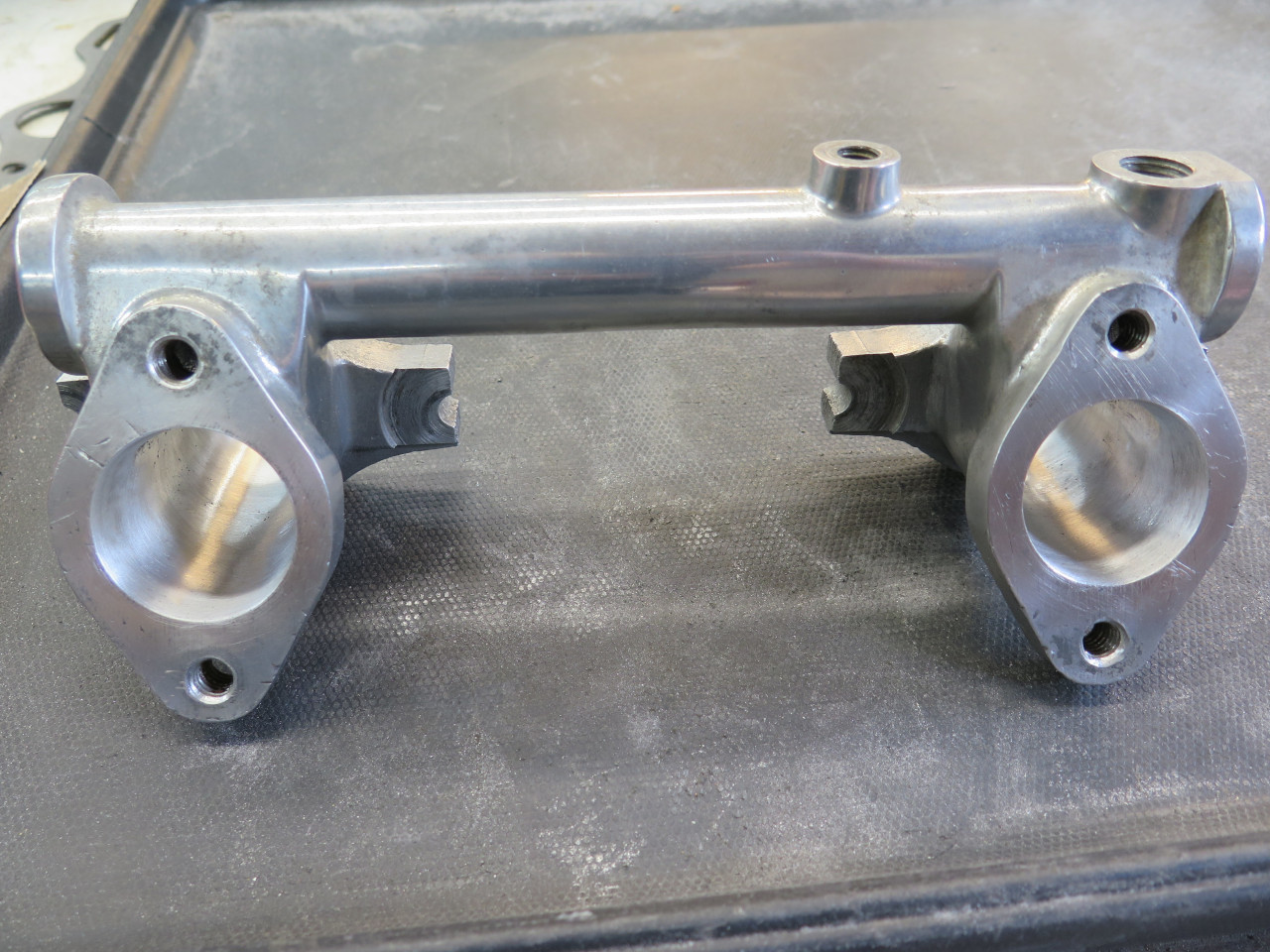
While in this mode, I wasn't even above making some admittedly cosmetic improvements, like this casting parting line.
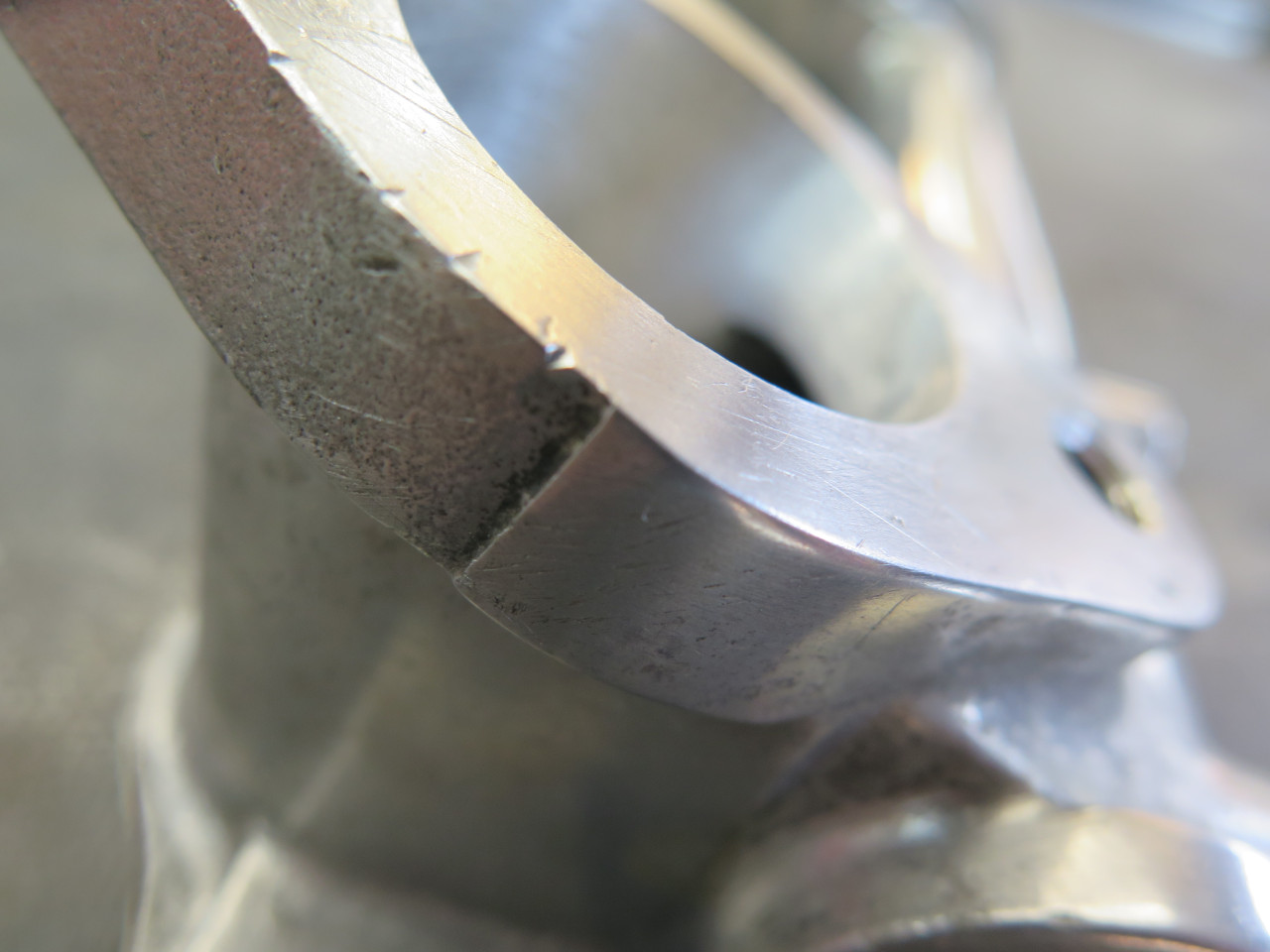
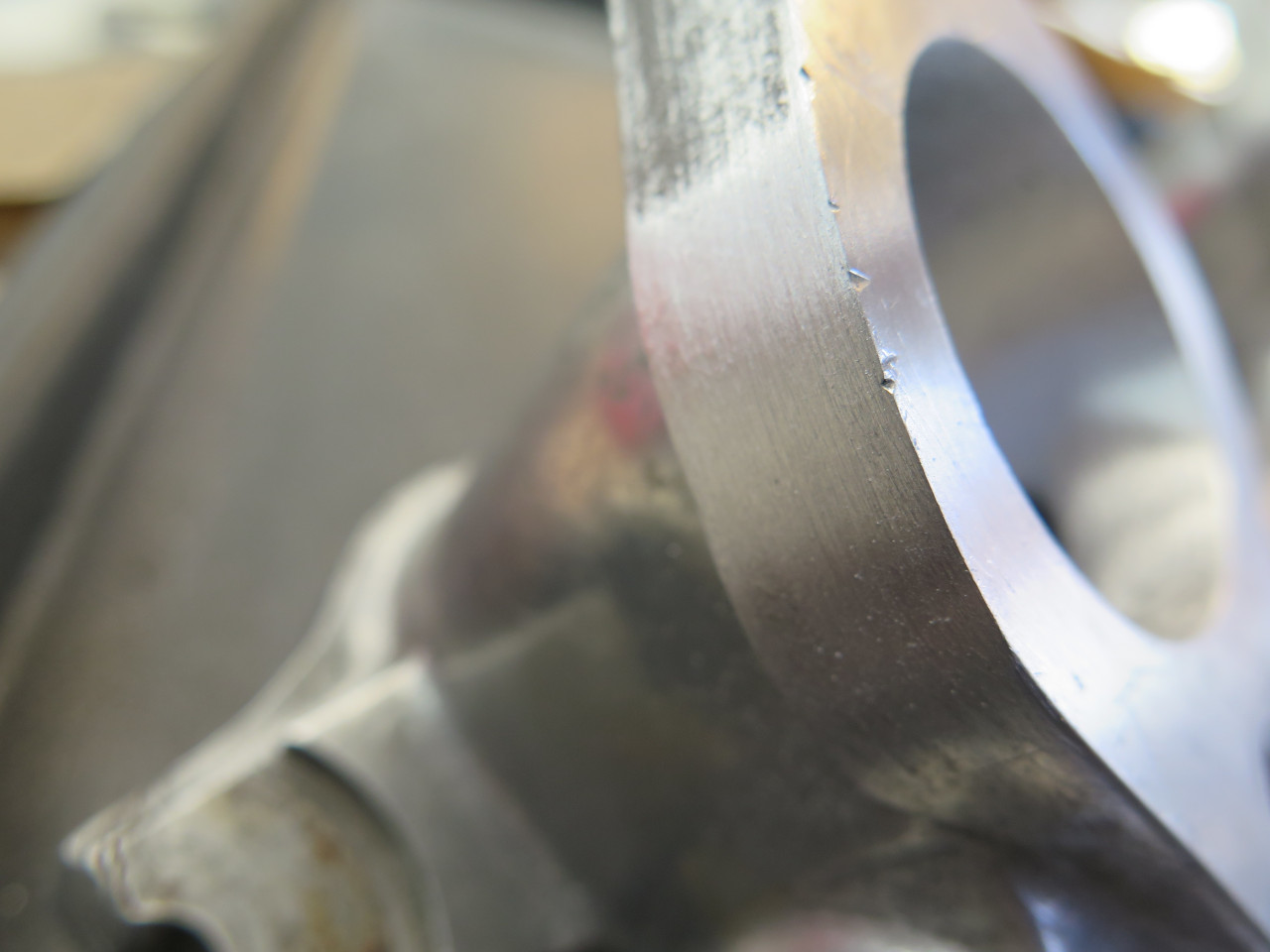
Then, on to more prosaic issues. The manifold's job is to pass
air/fuel mixture from the carbs to the head, and to preserve the
air/fuel ratio by not admitting any extraneous air. This means the
joints at the carbs and the head need to be air tight, and this is
facilitated by having the mating surfaces flat and coplanar.
A gross test for this is to place the mounting flanges on a known flat
surface, and check for rocking. Both sides of this manifold rocked
a little in this test. A feeler gauge can give a quantitative
measure.
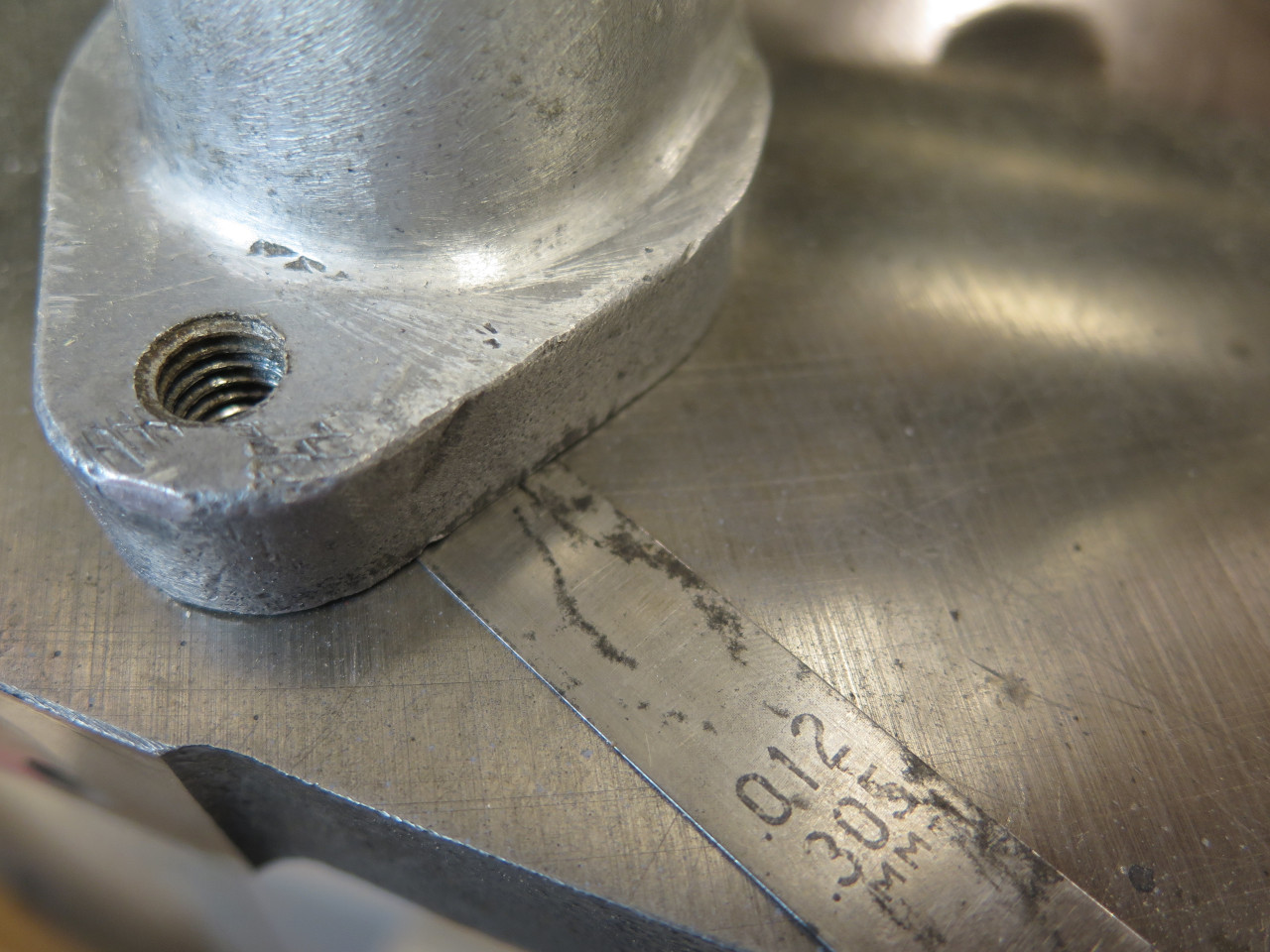
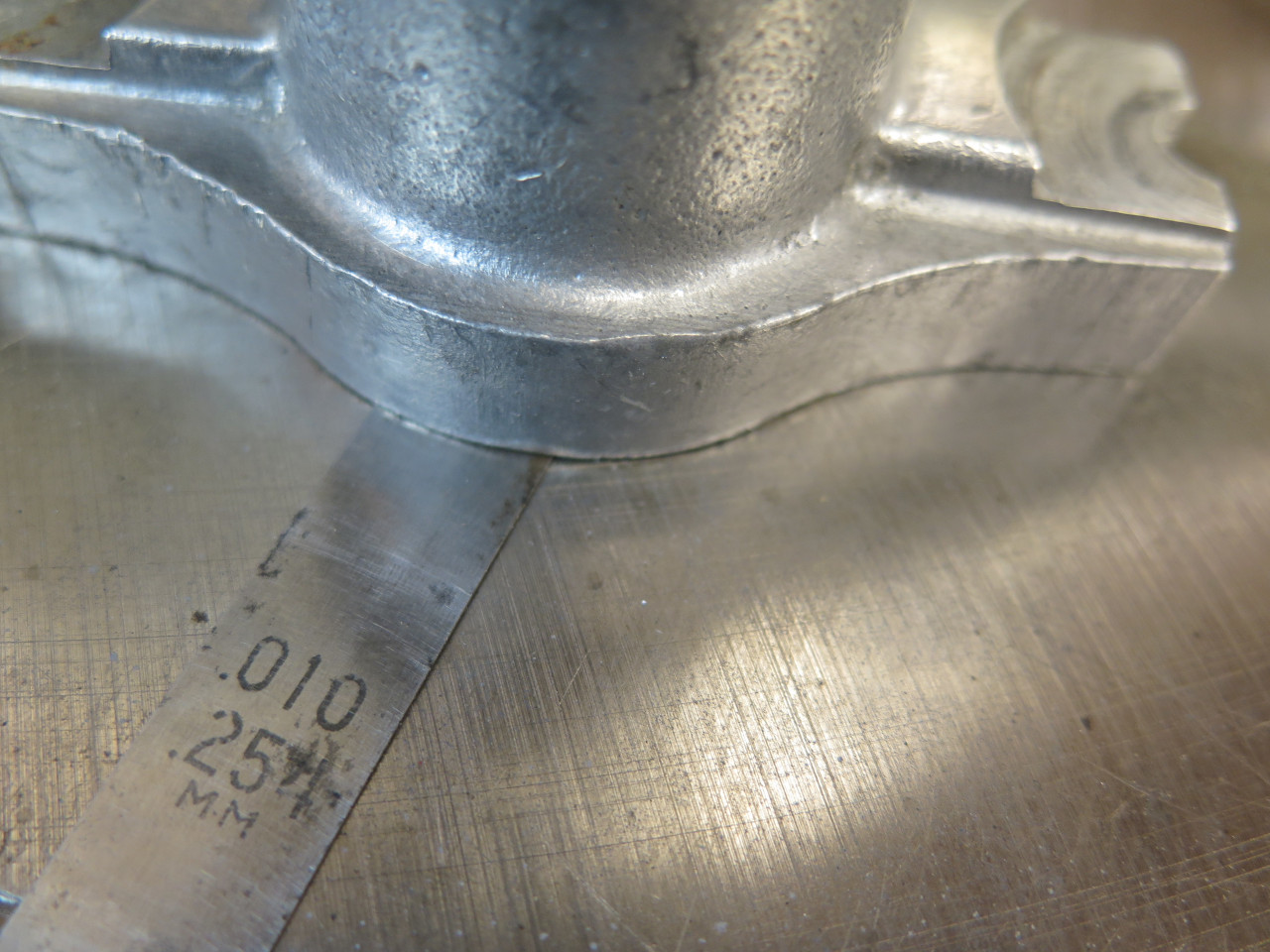
A little rubbing on some abrasive paper on a flat surface can show clearly where the high and low areas are.
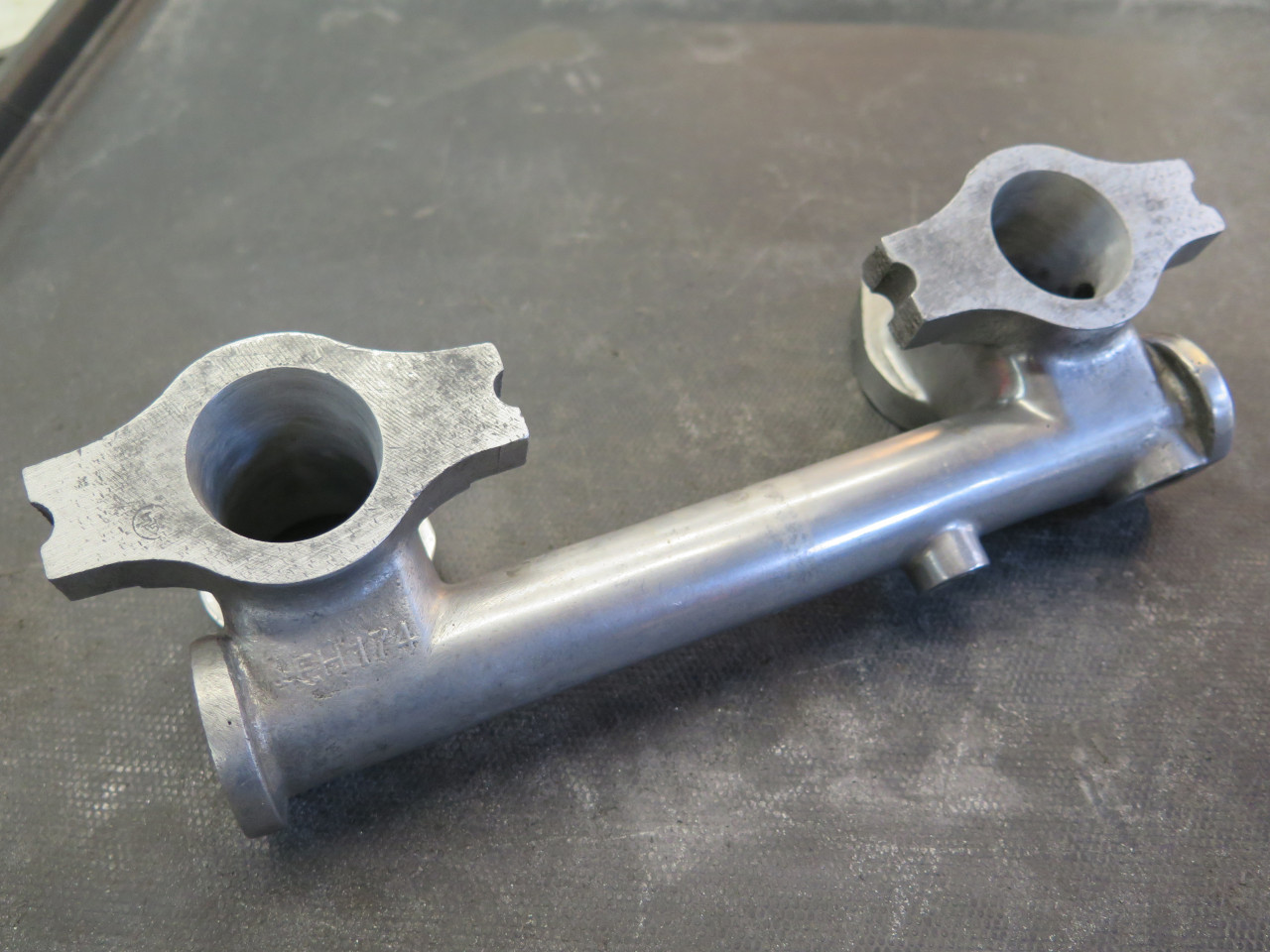
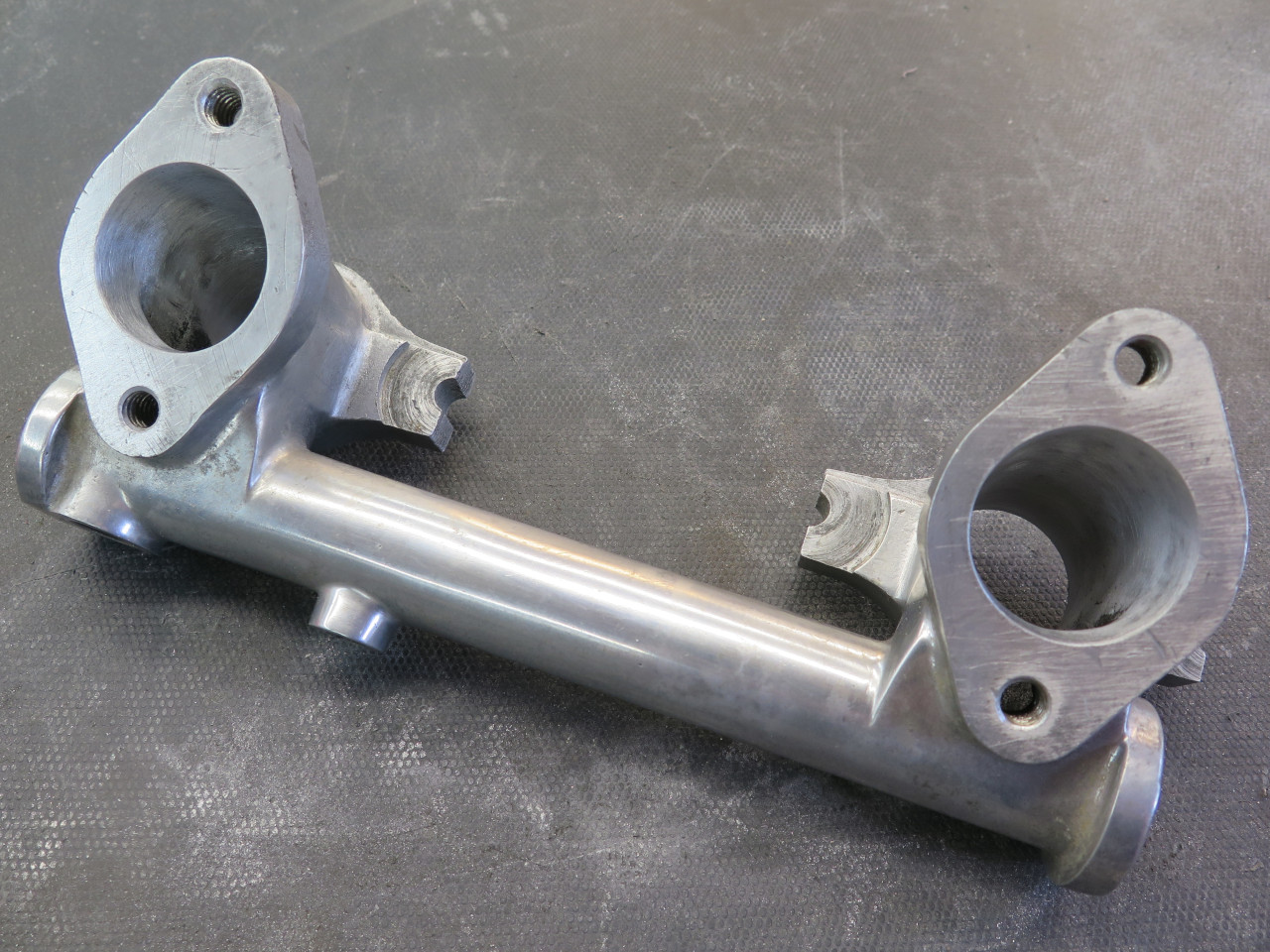
Would the gaskets accommodate this 0.010-0.012" non-flatness?
Probably, but why not start with flat flanges if you can. Besides,
both flanges had scars and scratches I really wanted to get rid of.
It took about 0.020" to fully clean up and flatten the carb side
flanges, and slightly less on the head side. One challenge was
that the inlet and outlet flange surfaces are not parallel. The carb
flanges are upturned by about 20 degrees.
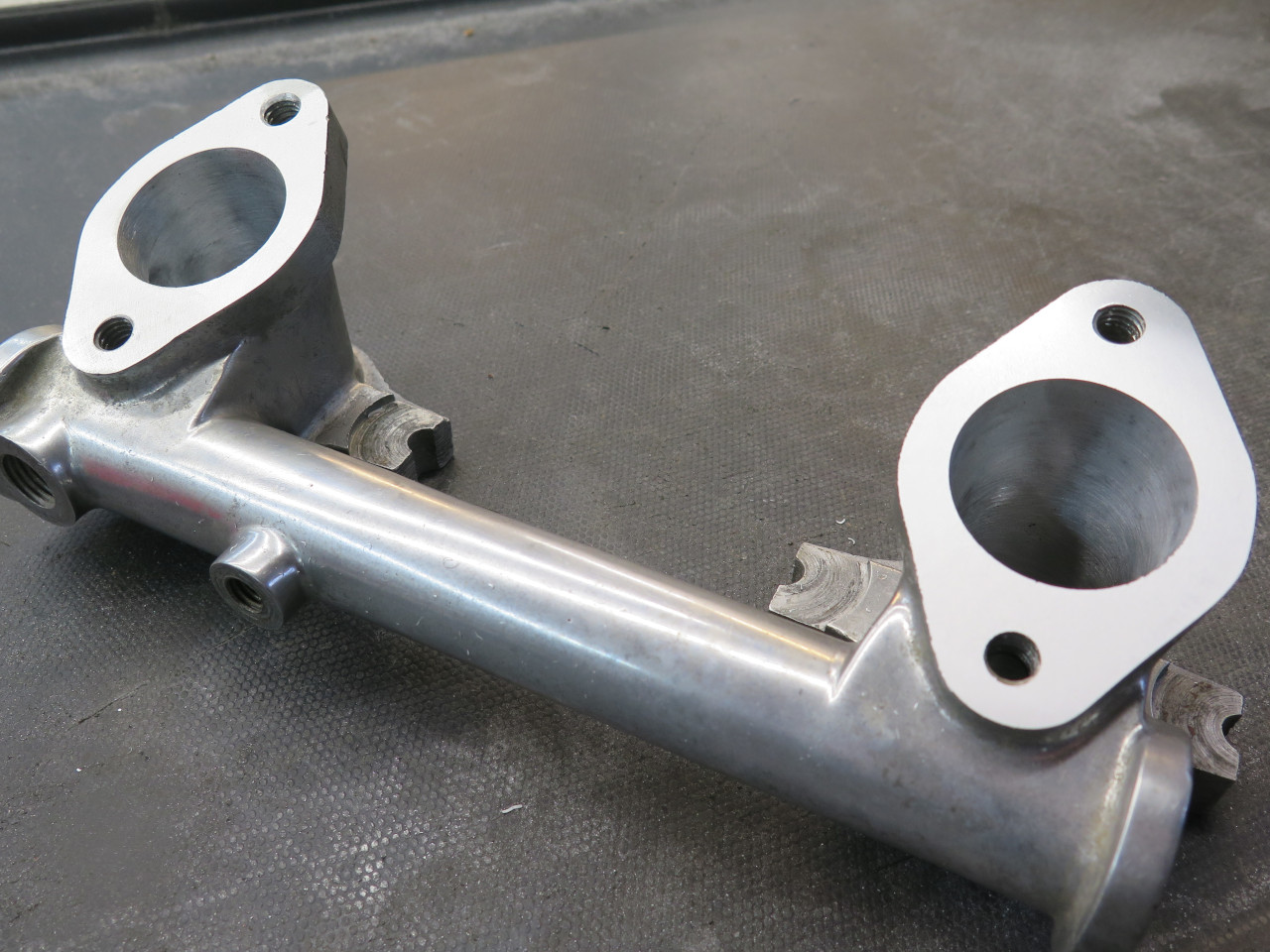
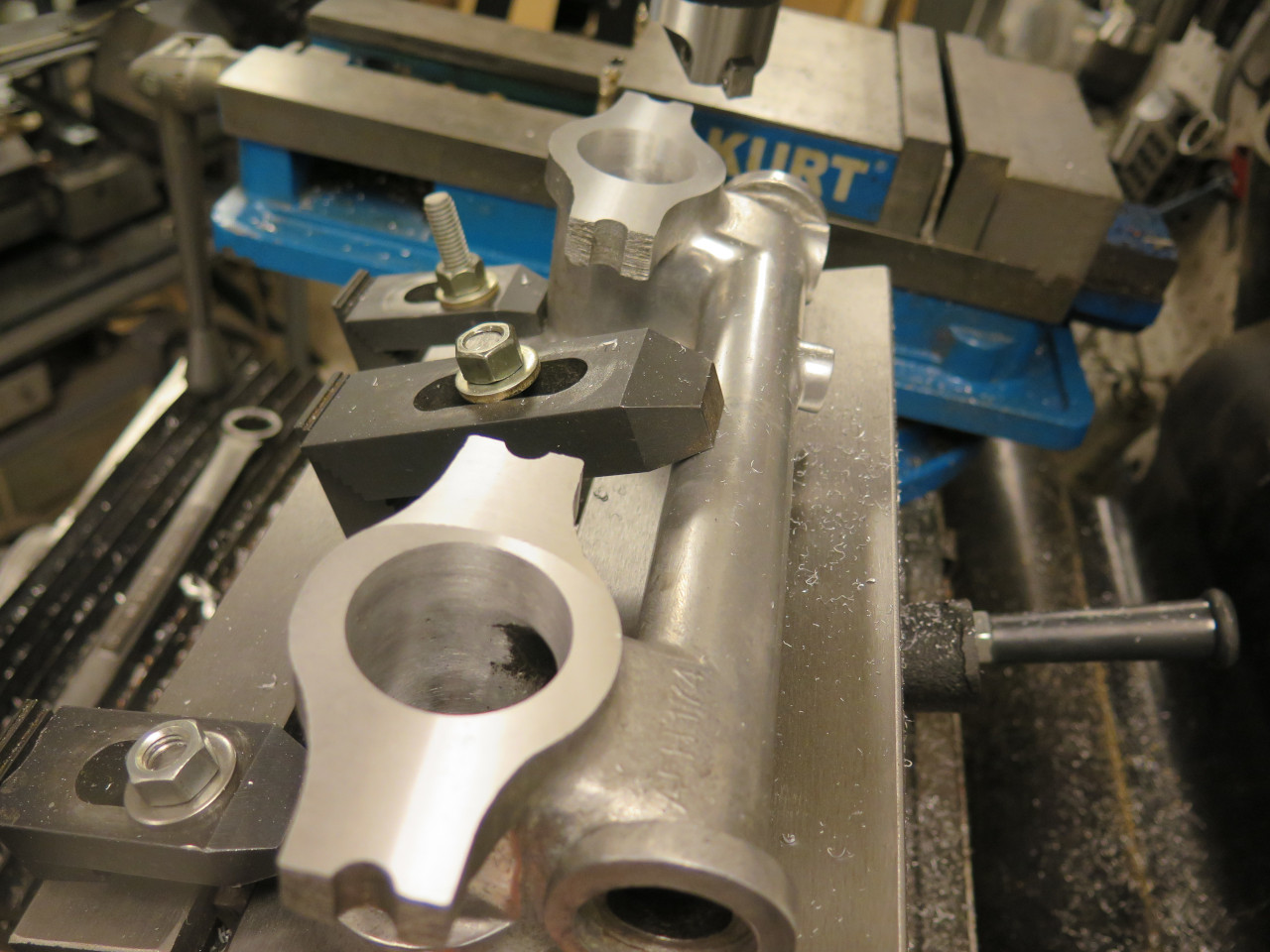
While I was at it, it was easy to clean up the ends of the head side flange, that looked like they'd been broken or sawed off.
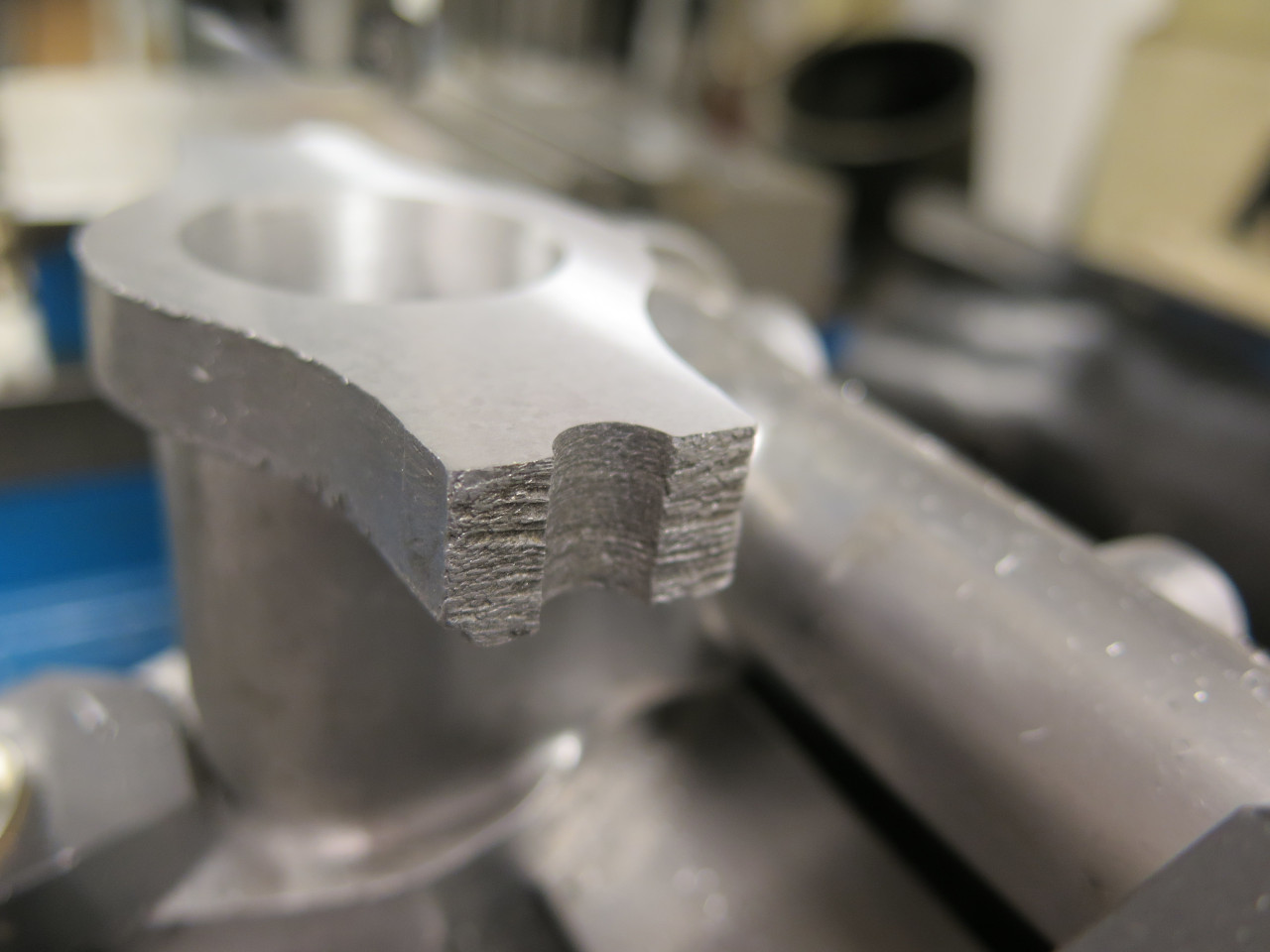
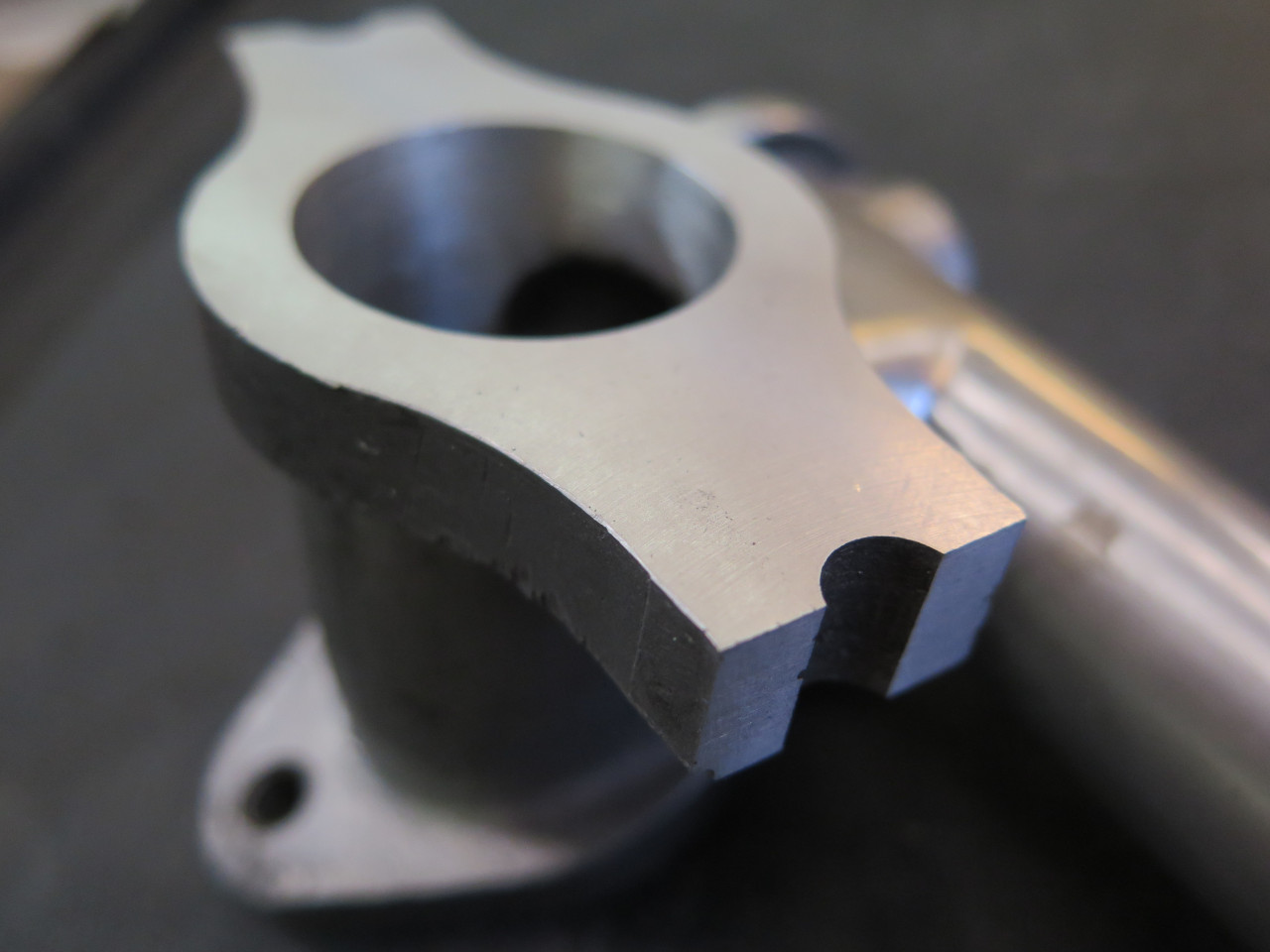
At some point, I had knocked out the core plugs at either end of the
balance tube, mainly because I knew I'd be doing a lot of grinding,
sanding, and milling on this part, and it would be way easier to get the
inside clean with them gone.
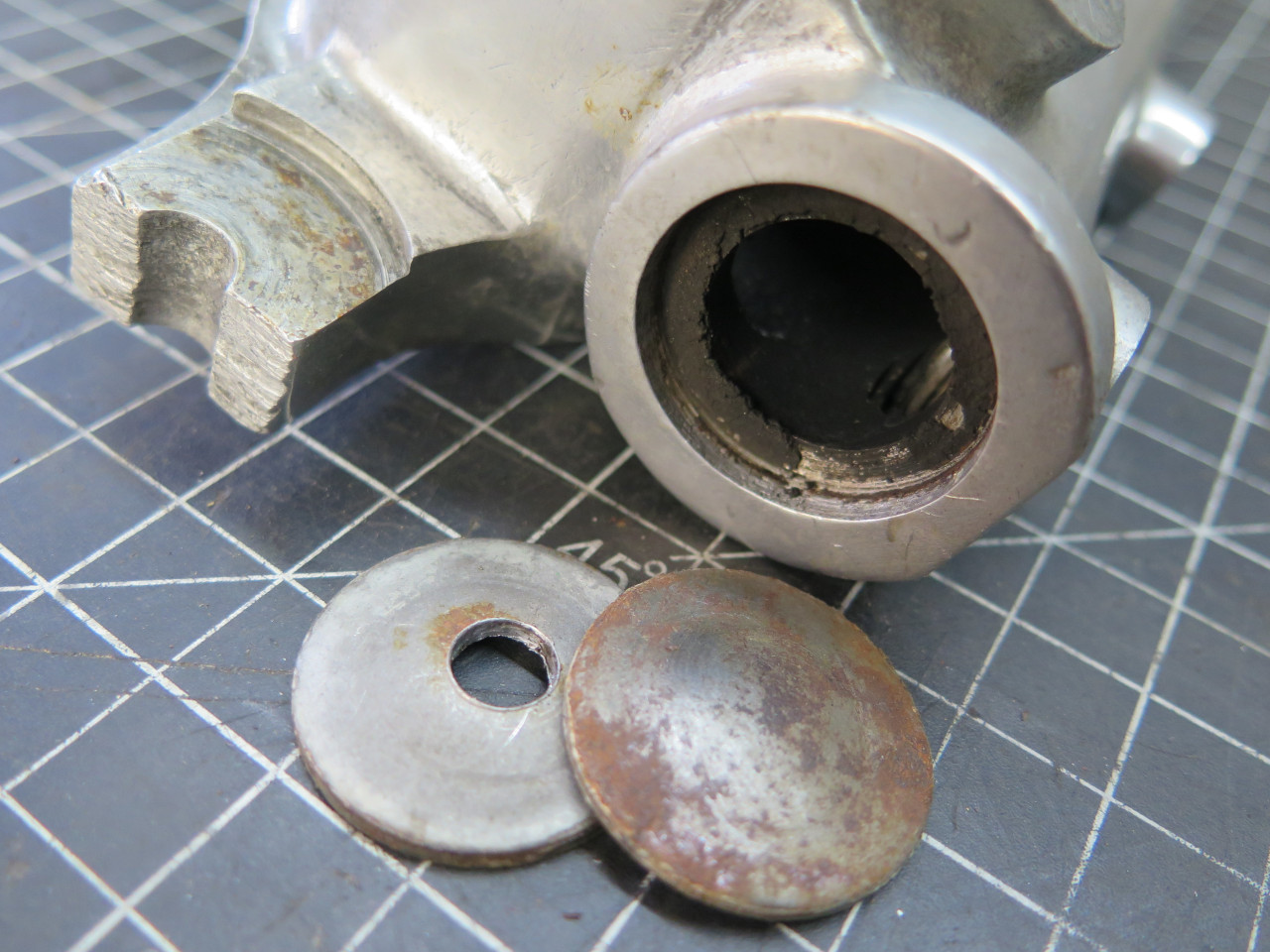
As for final surface finish, I know that I've matured a bit, and no
longer think that all aluminum parts need to be polished to a high
shine. On the other hand, I understand that this manifold was
likely painted engine color at the factory, and I haven't matured enough
to think that would look good.
So,as a middle ground, I decided to powder coat the manifold with a
"cast aluminum"color. One advantage of this over polishing is that
the surface would be consistent and uniform, even in areas where
polishing was just about impossible to do well.
First, a light grit blast for some tooth.
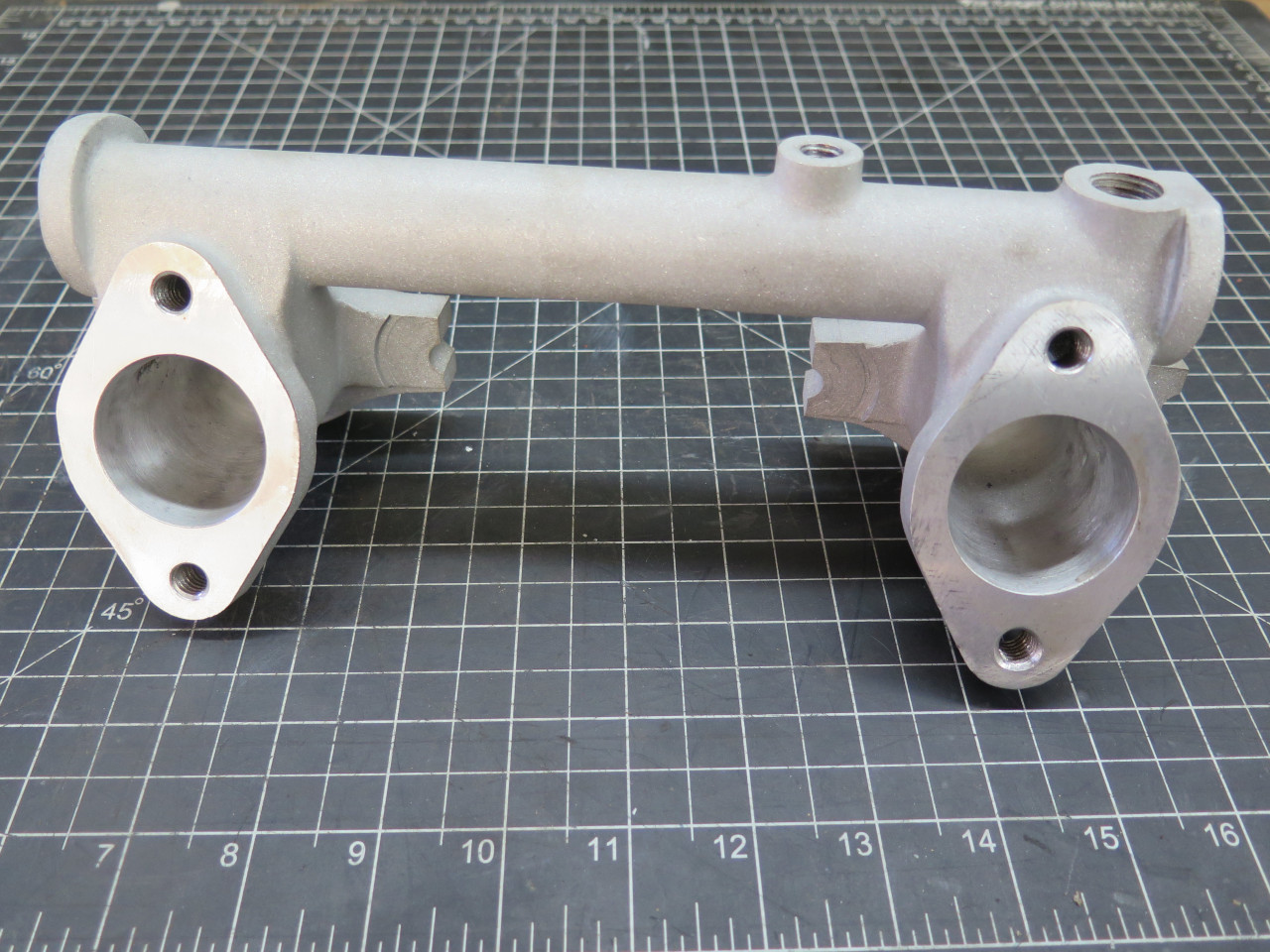
Then the powder coat.
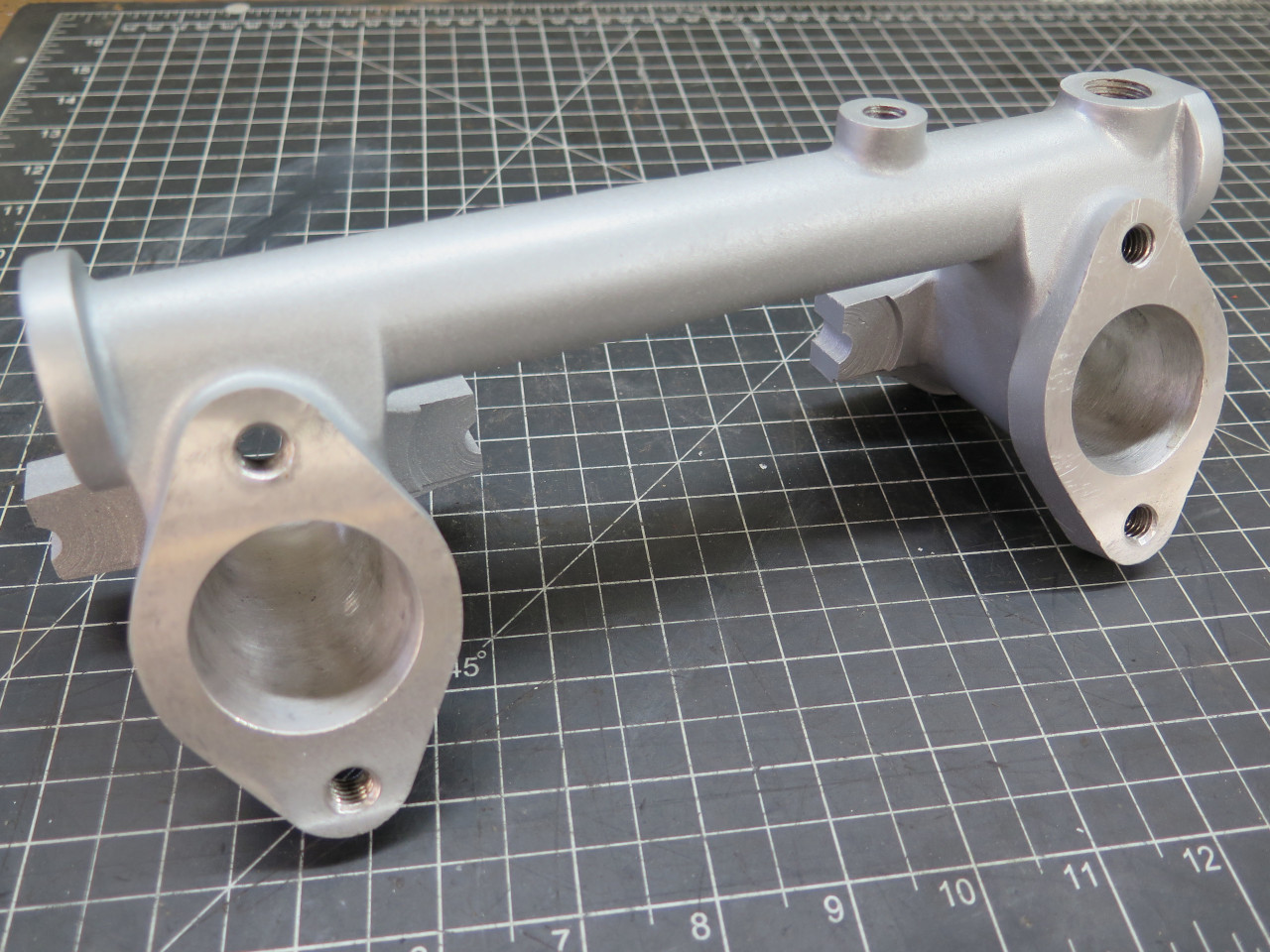
A pair of new stainless core plugs.
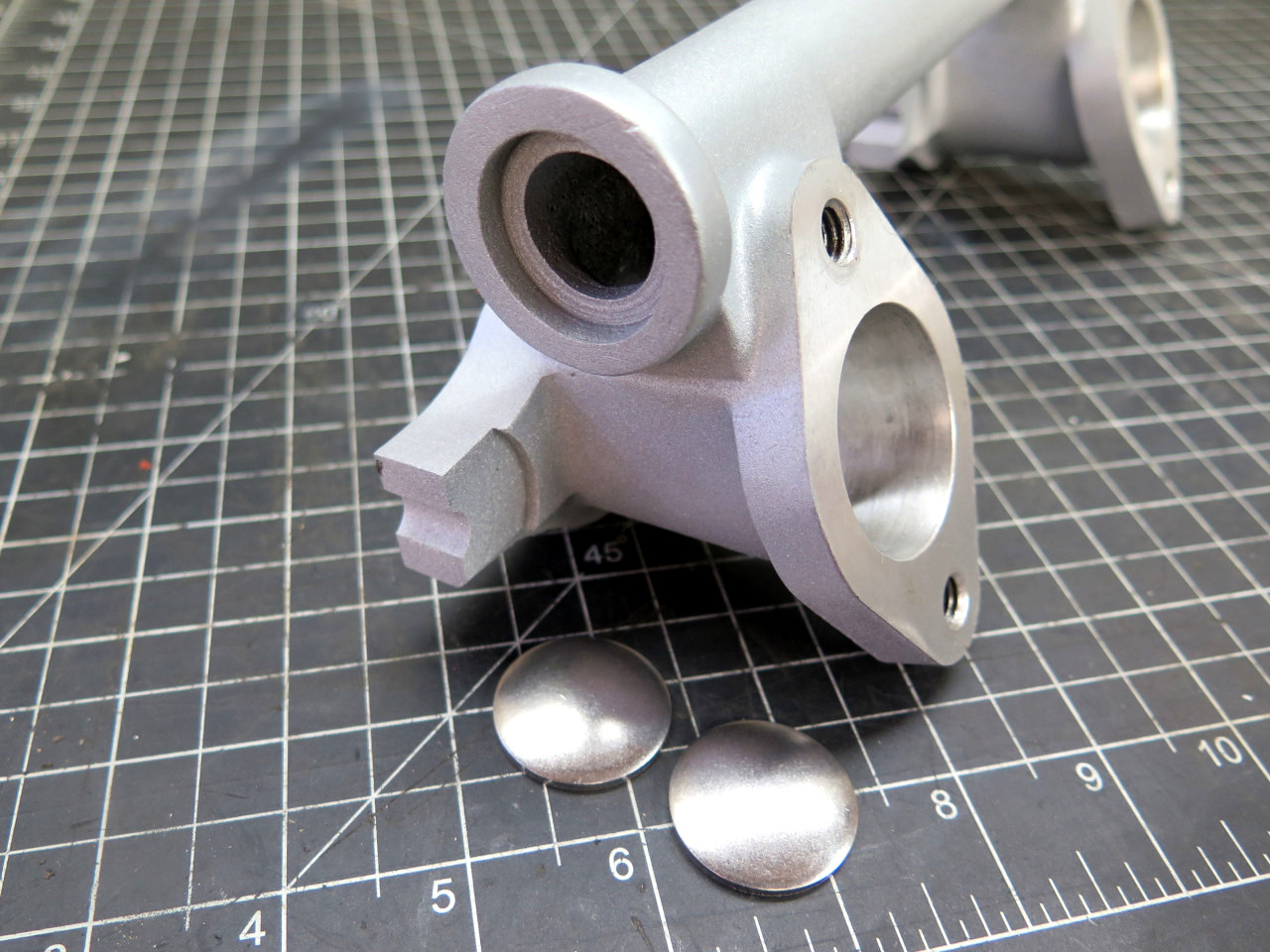

Replated studs. I had to make the one that goes into that little
adapter. Some of the studs are in holes open to the inside
passages, so they got some thread sealer.
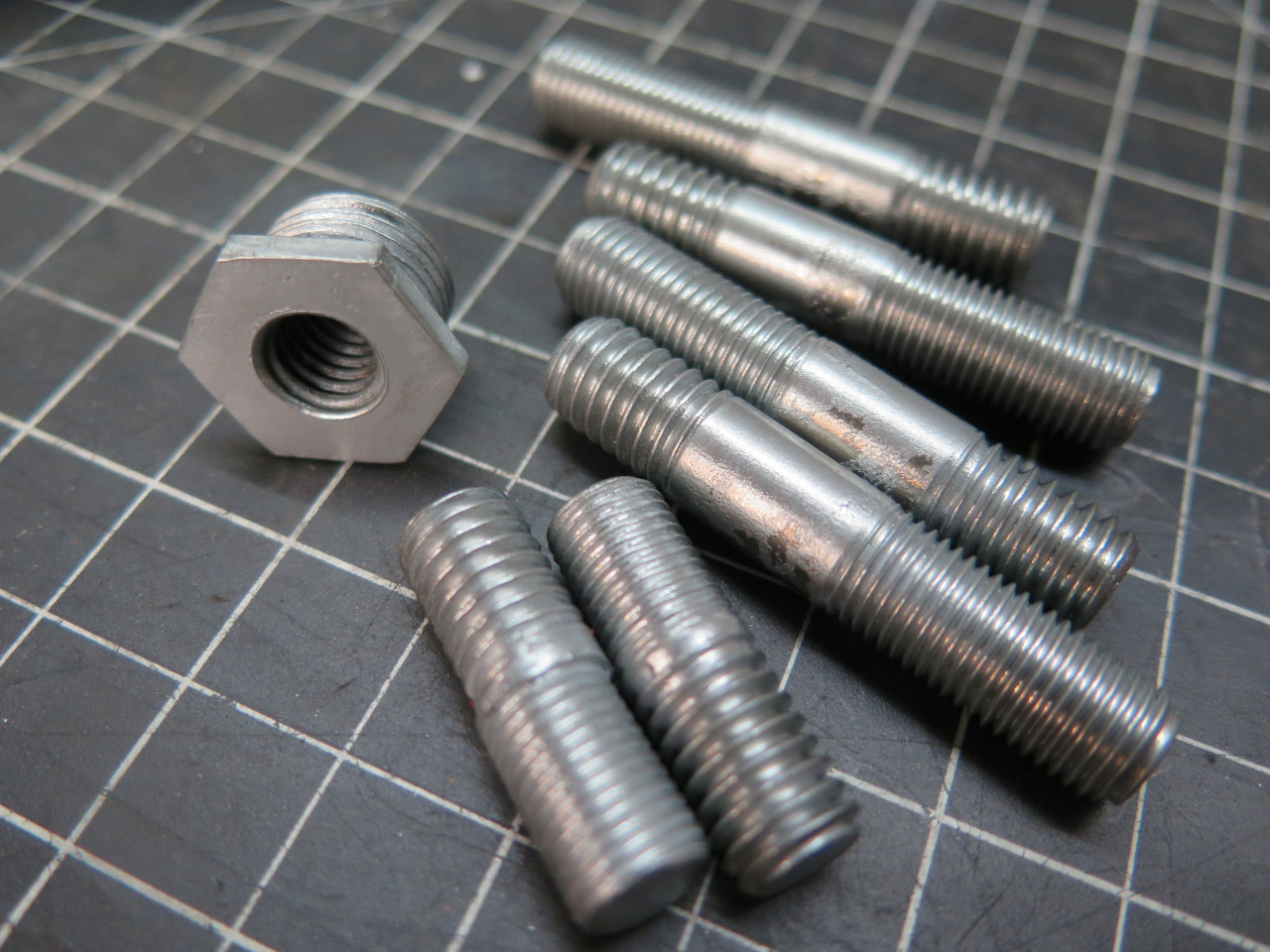
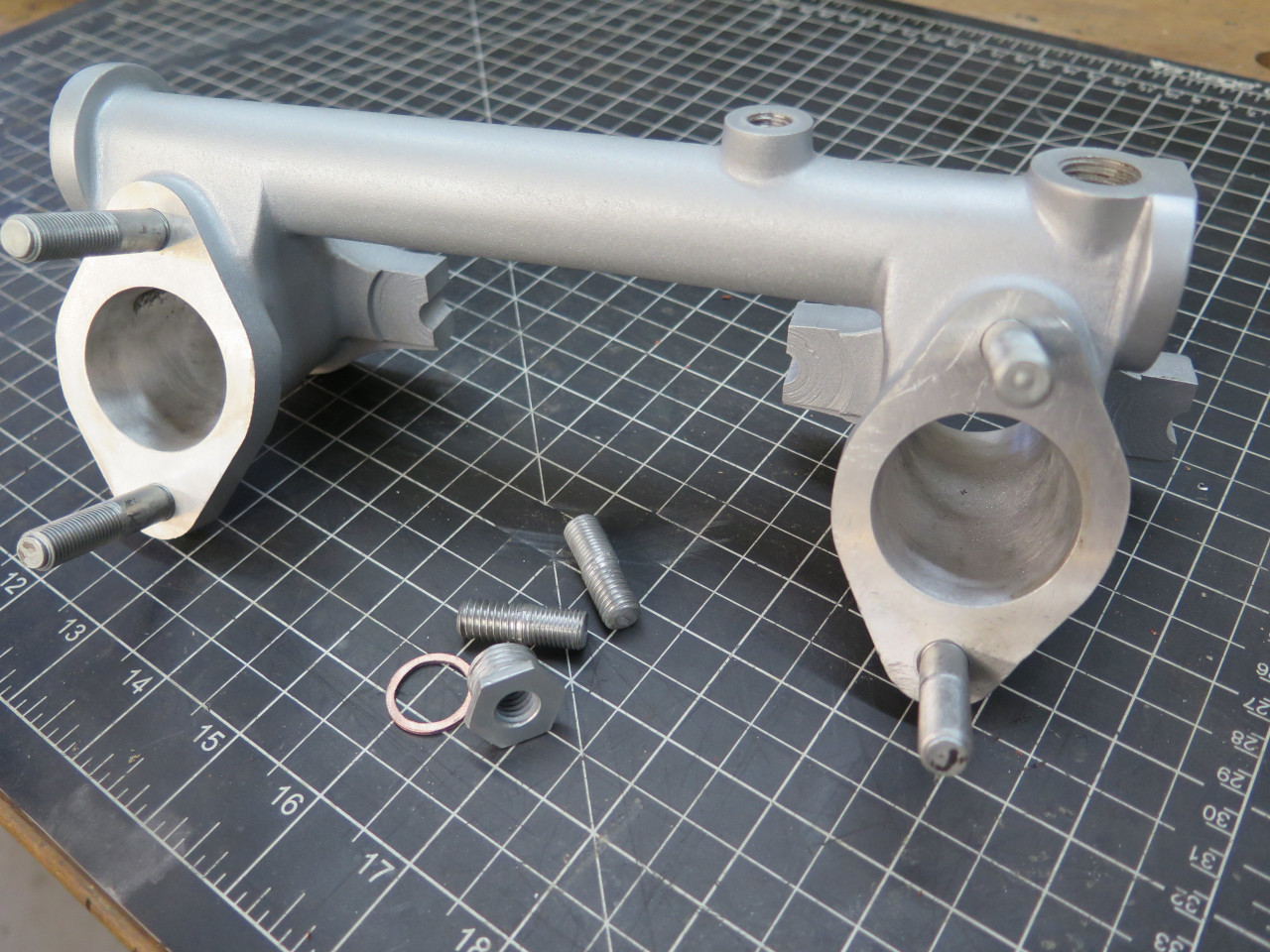
And on the shelf with this puppy.
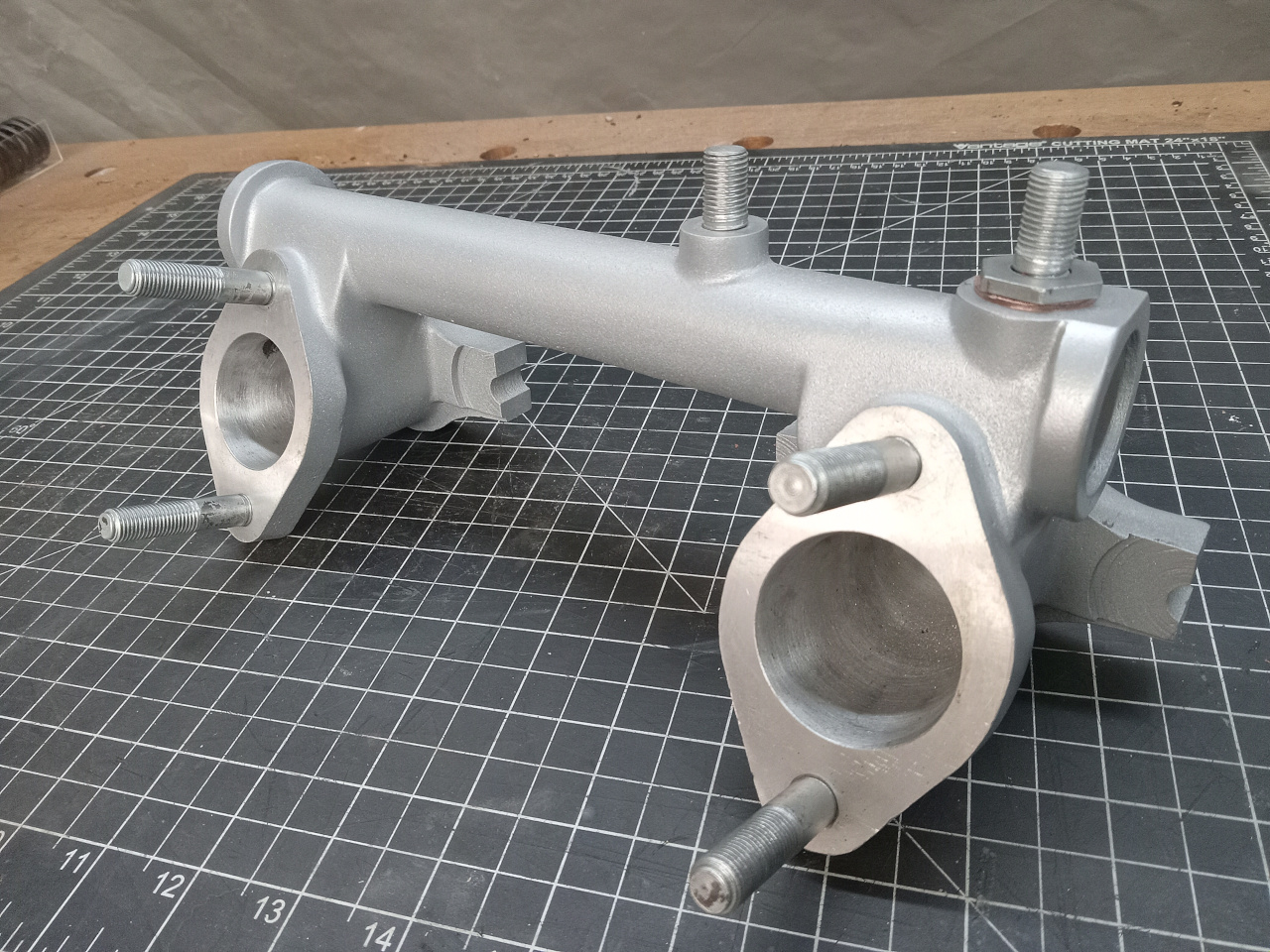
This was a pleasant, low stress job. It took a few days, and the cost was only a few dollars for the core plugs.
Comments to Ed at elhollin1@yahoo.com
To my other MGA pages